Torni per metalli & Co. Corso breve per vili genti meccaniche, bricoleurs e simpatizzanti.
In questa ultima lezione vediamo come sia possibile ottimizzare le condizioni di taglio, con particolare riferimento alla velocità di lavoro (chiamata anche di taglio) ed agli utensili impiegati.
La velocità di lavoro del tornio non è la velocità di rotazione del mandrino, bensì la velocità periferica del pezzo in rotazione montato sulla macchina. Quindi dipenderà non soltanto dalla velocità di rotazione, ma anche dal diametro del pezzo.
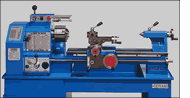
Potremo dire perciò che :
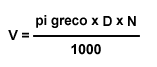
dove :
V è la velocità di taglio in mt/min
D è il diametro del pezzo in mm
N è il numero di giri/min del mandrino
Quindi, se sapremo quale V ci serve utilizzare, dalla formula di cui sopra ci sarà facile risalire a N, cioè al miglior valore possibile del numero di giri del mandrino.
Ma come si fà a sapere quali sono i valori di V da adottare ? La velocità di taglio dipende da molti fattori, principalmente dalla qualità del materiale da tornire, ma anche dal tipo di materiale del tagliente utilizzato nell' utensile, dal raffredamento dello stesso, dal valore degli angoli di taglio del tagliente, dalla sezione del truciolo, ed altri ancora.
La scelta della velocità di lavoro ha la massima importanza perchè da essa consegue il buon sfruttamento della macchina con il miglior rendimento possibile, anche in termini di minor tempo di esecuzione di un dato lavoro.
Personalmente però considero valido questo ultimo discorso prevalentemente in ambito professionale.
Noi hobbysti possiamo trascurare queste preoccupazioni, e quindi viene meno l' importanza della migliore velocità di taglio possibile. E' bene comunque conoscerla, soprattutto per non eccederla.
Qui sotto trovate una tabella che riporta per l' appunto le velocità di taglio per i materiali più comuni ed in funzione del materiale dell' utensile. I valori sono espressi in metri/min. I valori minimi sono quelli di sgrossatura, quelli maggiori di finitura.
| HSS | Widia |
Acciaio dolce [ferro] |
30-60 |
100-300 |
Acciaio duro, legato, bonificato |
20-30 |
40-150 |
Acciaio inox |
15-40 |
50-100 |
Ghisa |
|
|
Ottone e bronzo |
40-100 |
200-400 |
Leghe leggere |
60-200 |
200-500 |
Materie plastiche |
15-30 |
50-200 |
Ottone, bronzo e materie plastiche si lavorano senza lubrificazione.
Scelta la velocità di lavoro che interessa, per non perdere tempo a calcolare la velocità del mandrino per tornire un certo diametro del pezzo, è molto utile il cosiddetto "diagramma a ventaglio", molte volte riportato dal costruttore a bordo macchina. Se manca, è molto facile calcolarlo da sè medesimi.
Si prepara un diagramma cartersiano costituito da due scale ortogonali, una orizzontale ed una verticale.
Sulla scala orizzontale si riportano i diametri di tornitura. Ad esempio, da 0 a 150 mm in modo che ogni 10 mm della scala corrispondano a 10 mm di diametro del pezzo.
Sulla scala verticale si riportano le velocità di lavoro. Ad esempio, da 0 a 300 metri/min (ogni 5 mm della scala corrispondono a 10 metri/min).
Si annotano tutte le velocità di rotazione del mandrino. Si assume un diametro di tornitura arbitrario, ad esempio 50 mm. Ora, utilizzando la formula della velocità di lavoro, si calcola la velocità per un pezzo avente diametro 50 mm e tornito con la prima velocità del mandrino.
Ad esempio, se questa fosse 80 giri/min, la formula diventerebbe :
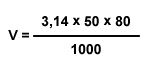
che dà come risultato 12,5 metri/min
Si riporta sulla scala orizzontale il valore di 50 mm, e su quella verticale 12,5 metri/min.
Si cerca il punto di incontro di due rette, una verticale innalzata dal punto 50 mm, ed una orizzontale partente a sinistra dal valore 12,5 metri/min.
Il punto d' incontro delle due rette si congiunge tramite un' ulteriore retta, (che risulterà leggermente inclinata ), al punto origine del diagramma. Questa retta è la retta "degli 80 giri/min".
Si ripete il lavoro per la seconda velocità del mandrino, (ad esempio 120giri/min), sempre utilizzando per i calcoli il diametro di 50 mm. Si otterrà una seconda retta, un po' più inclinata della prima, che sarà la retta "dei 120 giri/min".
Si completa per tutte le velocità di rotazione del tornio, ottenendo il diagramma a ventaglio completo, composto da tante rette inclinate aventi tutte un punto comune all' origine del diagramma ed aprentesi
a ventaglio.
Come si usa è intuitivo:
dato un certo diametro di tornitura, e fissata la velocità di lavoro, incrociando i due valori si otterà un punto sul diagramma. La retta inclinata che passa più vicino al punto è quella che individua i giri mandrino ottimali.
Spero di essermi spiegato con chiarezza !
Parliamo ora degli utensili.
Un corredo minimo è composto da uno sgrossatore destro, diritto ( 4971 D) o piegato che sia (4972 D), un finitore diritto (4975), un intestatore (4980 D), uno per gole (4981), due per filettare interno ed esterno (4985 e 4946) ed un troncatore, meglio se con barretta a fissaggio meccanico. Il resto secondo necessità, avendo presente che utensili di forma non unificata e comunque speciale possono essere agevolmente ricavati dalle usuali barrette in HSS lavorate alla mola.
Chi può spendere, o deve lavorare molto, oppure ha la necessità di lavorare materiali particolarmente duri e/o tenaci, può utilizzare utensili con placchette usa e getta in metallo duro fissate allo stelo meccanicamente.
E parliamo degli angoli di taglio dell' utensile, molto importanti per avere una buona resa della macchina ed un' ottima finitura. L' argomento è molto complicato da trattare senza poter affidarsi a rappresentazioni disegnate o fotografie, e quindi mi accontenterò del minimo indispensabile, trattando solamente gli angoli di taglio rappresentati su di un piano verticale.
Immaginate di guardare di fianco ed in sezione il pezzo da tornire e la punta dell' utensile :
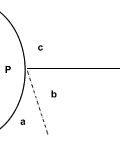
-P è il pezzo in tornitura
-"b" è l' angolo della punta dell' utensile che è a contatto con il pezzo da tornire P, angolo delimitato dalle due linee che rappresentano la superficie superiore ed inferiore del tagliente
-"a" è l' angolo compreso tra la superficie inferiore del tagliente ed una linea verticale tangente al diametro del pezzo
-"c" è l' angolo compreso tra la superficie superiore del tagliente ed una linea orizzontale
Nota : nel disegnino, "c" è uguale a zero, in quanto anche la superficie superiore dell' utensile è orizzontale. Normalmente, invece, gli utensili hanno la punta leggermente più alta verso il pezzo, e quindi
"c" ha un certo valore in gradi, in quanto la linea che rapprersenta la superficie superiore della punta dovrebbe, nel disegnino, risultare in realtà leggermente inclinata verso il basso da sinistra a destra.
Ebbene, questi 3 angoli sono importantissimi, e determinano le condizioni di lavoro dell' utensile.
Si chiamano :
"a" angolo di spoglia inferiore
"b" angolo di lavoro
"c" angolo di spoglia superiore
L' angolo di spoglia inferiore ha lo scopo di favorire il ritorno elastico del pezzo al cessare della pressione dello spigolo di taglio e di ridurre l' attrito di contatto.
L' angolo di lavoro favorisce la penetrazione dell' utensile nel pezzo, ma se il suo valore è piccolo riduce anche la robustezza della punta. Quindi l' angolo di lavoro sarà tanto più grande quanto più duro è
il materiale da tagliare. L' angolo di spoglia superiore ha la funzione di favorire l' avanzamento.
La tabella seguente indica i valori approssimati in gradi dei tre angoli di cui sopra in funzione del materiale da tagliare.
| "a" | "b" | "c" |
Acciaio dolce [ferro] |
6-10 |
55-65 |
20-25 |
Acciaio duro |
3-8 |
75-85 |
8-10 |
Ghisa |
2-3 |
85-88 |
0-6 |
Ottone e bronzo |
8-10 |
35-55 |
30-45 |
Leghe leggere |
8-12 |
45-60 |
15-25 |
In certi utensili a placchetta in widia il valore di "c" può essere di valore nullo od addirittura di valore negativo, cioè la punta dell' utensile non è inclinata verso l' alto, ma leggermente verso il basso.
Si tratta degli utensili "a spoglia negativa", utilizzati per lavorazioni ad alta velocità. Si adotta questo accorgimento perchè se l' angolo di spoglia superiore è negativo, l' angolo di lavoro diventa più grande, aumentando così la resistenza meccanica della placchetta.
Gli utensili si devono affilare con le mole appropriate (mole in carborundum per l' HSS, ed in carburo di silicio per il Widia).
Ora non vi rimane altro che avviare il motore del tornio ed iniziare il lavoro !
Cordialità.
Per mia informazione ditemi comunque se le spiegazioni sono comprensibili anche a chi, pur avendo interesse all' argomento, non mastica molto in termini tecnici. Mi servirà, se possibile, per adeguarmi nel prosieguo di queste brevi note.
Cordialità.
[Lezione N.1] - [Lezione N.2] - [Lezione N.3] - [Lezione N.4]
Nota: By: Paul (paulhass@tiscalinet.it)