Torni per metalli & Co. Corso breve per vili genti meccaniche, bricoleurs e simpatizzanti.
Proseguiamo nella descrizione delle parti costituenti un tornio parallelo, già iniziata nel messaggio precedente.
Quando avremo così imparato la nomenclatura dei varii componenti,ci sarà più facile, e con maggiore cognizione, discutere delle lavorazioni propriamente dette.
Avevamo visto il bancale, la testa, la scatola degli avanzamenti,i carrelli, la torretta portautensili.
Parliamo ora della "controtesta", delle "lunette", degli "organi di presa"dei pezzi in lavoro, e
dell' "impianto refrigerante".
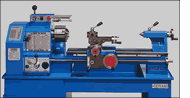
La controtesta è il spporto mobile posizionato a destra della macchina, scorrente manualmente sulle guide del bancale, che fà da sostegno alla "contropunta". Quest' ultima è contenuta in una sede conica di
una bussola la quale è impegnata con una vite che può venir manovrata con un volantino. La contropunta ha la caratteristica di essere alla stessa altezza dell' asse del mandrino, e quindi di poter servire a
sostenere l' estermità destra del pezzo in lavoro (se lungo), mentre l' estremità sinistra del pezzo è sostenuta dal lato del mandrino.
In tal modo il pezzo potrà ruotare con l' asse perfettamente orizzontale.
Per altre lavorazioni (ne parleremo più avanti), la contopunta può essere sostituita nella controtesta da un codolo portante un mandrino a cremagliera da trapano, attrezzabile con le usuali punte elicoidali
oppure con speciali "punte da centro". Girando il volantino della controtesta si fà avanzare la punta che forerà centralmente il pezzo che ruota trascinato dal mandrino.
La controtesta, che come già detto porta la contropunta perfettamente allineata in altezza con l' asse della macchina, può in certi casi essere spostata con una chiave di manovra di una piccola entità in direzione trasversale alle guide del bancale. In tal modo l'asse di rotazione del pezzo non sarà più parallelo alle guide del bancale, e così si potranno realizzare torniture di debole conicità.
Vi risparmio la formula matematica che sapendo la lunghezza e il diametro maggiore e quello minore del pezzo da tornire conico, consente di conoscere l' esatto valore dello spostamento che si deve dare alla controtesta.
Per torniture coniche con angolazioni molto forti, invece, si adotta un metodo differente, del quale parleremo in seguito.
Se il pezzo in lavorazione è di diametro ridotto e molto lungo,non è sufficiente sostenerlo alle sue due estremità, perchè sotto la pressione dell' utensile di taglio fletterebbe, e la tornitura darebbe luogo ad incostanza di diametro finito, oppure il pezzo stesso scavalcherebbe la punta dell' utensile. E' perciò necessario sostenerlo anche nei pressi dove si esercita la pressione di lavoro.
Questo compito è assicurato dalle "lunette" , che sono costituite da una base fissabile alle guide del bancale (lunetta fissa), oppure fissabile al carrello (lunetta mobile), e da un cappello apribile a cerniera. Aprendo il cappello si inserisce dentro la lunetta il pezzo da lavorare, che sarà sostenuto da tre blocchetti in acciaio con superfici di appoggio rettificate e regolabili radialmente a mezzo di viti.
Un' altra possibile applicazione della lunetta fissa è quando un pezzo cilindrico e lungo, (che quindi per il piazzamento in macchina deve essere sostenuto a destra dalla contropunta), non ha la possibilità di essere forato in centro per l' alloggiamento della punta stessa.
In tal caso, la parte destra del pezzo si alloggia nella lunetta fissa, posizionata in luogo della controtesta. Naturalmente in questo caso il centraggio del pezzo deve essere fatto a mano, preferibilmente
con un comparatore.
Se non avete capito come funzionano le lunette, consolatevi sapendo che il loro uso è molto sporadico e quindi raramente le usereste !
Parliamo ora degli organi di presa del pezzo, cioè di quei dispositivi che servono a bloccare il pezzo in lavoro e contemporaneamente a trasmettere allo stesso il moto di rotazione.
Possono essere :
- piattaforma autocentrante (per montaggio a sbalzo)
- piattaforma a morsetti liberi ( " " " " )
- spina di trascinamento (per montaggio tra le punte od a sbalzo)
- disco menabrida (per montaggio tra le punte)
- pinza concentrica ( " " a sbalzo)
- plateau (per montaggio a sbalzo)
La piattaforma autocentrante, (o semplicemente "autocentrante") chiamata impropriamente anche "mandrino", è il dispositivo di presa che è maggiormante usato. Funziona come un mandrino da trapano,
nel senso che è formata da un corpo cilindrico portante 3 o 4 griffe a gradini (chiamate anche "cani" o "morsetti"), che possono simultaneamente convergere od allontanarsi radialmente dal centro della piattaforma, manovrati da una apposita chiave.
Ruotando la chiave, i morsetti stingeranno fortemente il pezzo e lo porranno in rotazione all' avviamento della macchina.
Per aumentare la possibilità di presa, le griffe sono di 2 tipi : per serraggi interni e per esterni. Il tipo di griffe quindi si sceglie in base al diametro del pezzo da fissare, ed alla possibilità di presa sul pezzo.
Quando si sostituisce un tipo di griffe con l' altro, svincolandole dalle loro guide, ricordarsi che ciascuna griffa è numerata, e perciò deve essere accoppiata solo con la guida corrispondente.
L' autocentrante è un organo costruito con grande precisione, con tolleranze centesimali, e dalla sua bontà deriva buona parte dell' accuratezza di lavoro.
Quindi và trattato con riguardo, soprattutto se e quando deve essere smontato e rimontato dall' asse del mandrino. Niente martellate, perciò.
La piattaforma a morsetti liberi è simile all' autocentrante, ma le singole griffe devono essere manovrate indipendentemente l' una dall' altra. Serve perciò per fissare pezzi a sezione differente da quella circolare o addirittura non simmetrici. E' molto utile se per caso devono esse fatte delle torniture eccentriche, sebbene queste possono essere fatte anche sull' autocentrante, interponendo un adeguato spessore tra una sola griffa ed il pezzo.
Se si deve tornire dei pezzi simili a dischi forati, che non possono essere trattenuti sulle piattaforme a causa del ridotto spessore, si fà ricorso alle spine di montaggio. Queste sono degli alberi di adeguato diametro, a volte conici, altre volte muniti di convenienti battute per l' appoggio dei pezzi, che vengono costruiti sullo stesso tornio e/o adattati di volta in volta secondo necessità. Le spine, dopo che su di esse è stato provveduto il montaggio del pezzo, a loro volta sono fissate in macchina.
Un tipo semplicissimo di spina già pronta, adatta al montaggio a sbalzo, è una vite di conveniente diametro sulla quale il pezzo viene fissato stringendolo con due dadi.
Il disco menabrida è un sistema ormai che non si usa più, salvo casi speciali come la tornitura a debole conicità di pezzi lunghi montati tra le punte. Si tratta di un disco montato sull' albero del mandrino, che
porta un perno sporgente. Sul pezzo da lavorare viene fissata la "brida", che è una specie di anello con un codolo. Quando si pone in rotazione il disco menabrida, il perno fissato allo stesso impegna il codolo della brida ponendo in rotazione il pezzo sul quale la stessa è fissata.
Piccoli torni, come quelli di precisione per minuterie, o per orologiai, hanno come organo di presa del pezzo (che in questi casi è sempre a sezione tonda), una pinza concentrica di adeguata misura, che assicura maggior precisione di centraggio e rapidità di serraggio. Ma sono da considerare già fuori dall' interesse del bricoleur, e li nomino solo per completezza d' informazione.
Come ultimo sistema di fissaggio ricordo il "plateau", che altro non è che una piattaforma a disco sulla faccia piana della quale sono ricavate per fresatura delle cave che accolgono le teste delle viti stringenti dei morsetti a forma libera che bloccano il pezzo in lavoro.
Qualche volta le funzioni di piattaforma a morsetti liberi e di plateau sono integrate in un unico articolo.
Il plateau si usa quasi sempre per operazioni di sfacciatura di pezzi con forma articolata, ed in tal caso il tornio diventa in pratica una fresatrice in piano, dove il lavoro della fresa a spianare è sostituito
dall' azione dell' utensile del tornio.
Per quanto riguarda l' impianto refrigerante, cominciamo col dire che nei piccoli torni hobbystici manca del tutto.
La necessità di usare gli appositi olii da taglio nella lavorazione, infatti, è più sentita in ambito professionale, dove si lavora con alte velocità di taglio e con forti passate di utensile, specie con metalli
ferrosi, e quindi si sviluppano per attrito temperature non indifferenti.
In tal caso un' elettropoma centrifuga che pesca in un serbatoio riempito con una emulsione di acqua ed olio da taglio, invia ad un beccuccio erogatore posto sopra l' utensile un getto che ha funzioni lubrificanti e
refrigeranti.
Il liquido si raccoglie poi nella vasca dei trucioli posta sotto le guide del tornio, e per gravità torna nel serbatoio passando in un opportuno condotto. Se nel vostro tornio non è previsto questo impianto,
per consolarvi vi dirò che, oltre che raccogliersi nella vasca, l' emulsione oleosa schizza un po' anche sull' operatore e sul pavimento.
Oltre tutto, l' emulsione oleosa stazionante nel serbatoio si ossida con il tempo e viene anche attaccata da batteri che la rendono di odore sgradevole.
Forse vi ho già convinto a lavorare, se possibile, a secco !
Alla prossima i principali tipi di lavorazione eseguibili al tornio.
Per mia informazione ditemi comunque se le spiegazioni sono comprensibili anche a chi, pur avendo interesse all' argomento, non mastica molto in termini tecnici. Mi servirà, se possibile, per adeguarmi nel prosieguo di queste brevi note.
Cordialità.
[Lezione N.1] - [Lezione N.2] - [Lezione N.3] - [Lezione N.4]
Nota: By: Paul (paulhass@tiscalinet.it)