Un materiale composito è il risultato dell’unione di due o più materiali, suddivisi tra fibre, matrici ed additivi. É di fatto l’unione di più forze ognuna delle quali apporta la propria caratteristica chimico fisica, al fine di ottenere un materiale con proprietà e prestazioni superiori, non ottenibile dai costituenti presi singolarmente.
I materiali compositi più conosciuti presenti sul mercato sono:
- Compositi a matrice organica o polimerica (laminati, plastiche rinforzate, vetroresine)
- Compositi a matrice inorganico o minerale (calcestruzzo e i compositi ceramici)
- Compositi a matrice metallica (composti da allumina, grafite e carburo di silicio con fibre di Carbonio)
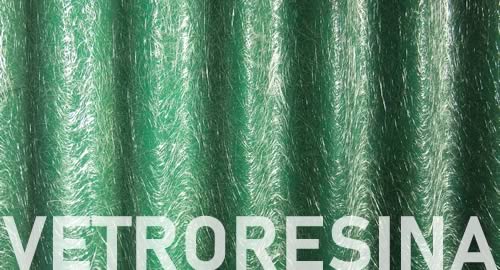
Oggigiorno, quando si pensa ai materiali compositi, spesso ci si riferisce a quelli di ultima generazione, i cosiddetti materiali fibrorinforzati, compositi a matrice polimerica i cui componenti principali sono costituiti dalle fibre e dalle resine. La fibra, grazie alle elevate proprietà meccaniche, è la parte che costituisce il rinforzo vero e proprio: è quella che induce rigidità e forza al composito. Le più diffuse sono le fibre di carbonio, di vetro e aramidiche (kevlar). Da sola la fibra non è in grado di assumere una forma vera e propria. Per poter essere sagomata ha bisogno di essere impregnata da una matrice indurente: la resina per l’appunto.
Ma il compito della resina va ben oltre a questo. Le resine influenzano soprattutto le proprietà di un composito, e seppur le loro caratteristiche meccaniche siano inferiori a quelle delle fibre, il connubio tra i due materiali conferisce al materiale composito ottenuto resistenza e durabilità nel tempo. Da ciò ne deriva che la scelta del tipo di fibra da utilizzare (fibra di vetro o di carbonio) è tanto importante quanto quella della resina e degli additivi da incorporare.
I compositi fibrorinforzati: la vetroresina
La maggior parte delle applicazioni dei materiali compositi organici (o fibrorinforzati) in matrice polimerica utilizzano la fibra di vetro come base di rinforzo con l’aggiunta di resina polimerica (poliestere, vinilestere o epossidica), come matrice, che oltre a proteggere la fibra, fa lavorare in modo omogeneo tutti i suoi filamenti.
Questa categoria di compositi, comunemente detta vetroresina, vede il giusto connubio tra la resistenza al carico di compressione conferito dalla resina e la resistenza alla trazione dato dalla fibra di vetro. La vetroresina è un materiale composito trasparente, leggero, duraturo nel tempo, resistente agli urti, che ben sopporta gli eventi atmosferici e resiste ai raggi UV. La vetroresina garantisce bassa conducibilità elettrica e termica, è un composito atossico e in particolare, non richiedendo una specifica manutenzione, limita i costi di esercizio.
Grazie alle sue molteplici proprietà, la vetroresina si adatta bene ad essere impiegata in diversi tipi di lavorazioni nel settore edile (isolamento delle abitazioni), in quello della filiera automotive (nella realizzazione di componenti per autoveicoli), nel settore nautico (creazione degli scafi delle imbarcazioni), in quello agricolo (realizzazione di cisterne) ed in ultimo, ma non per ultimo, nel settore aerospaziale.
A cosa servono le resine nella produzione della vetroresina?
Le resine hanno il compito di tenere allineate le fibre, di proteggerle e di distribuire il carico su tutta la struttura. Tutti i materiali compositi condividono forza, leggerezza, rigidità e resistenza agli ambienti difficili. Queste proprietà possono essere rese dominanti l’una sull’altra in base alla scelta della resina più idonea, per questo motivo è fondamentale conoscere le loro caratteristiche per scegliere quella più appropriata.
Cosa sono le resine polimeriche (polimeri)
Le resine polimeriche sono resine che si presentano in forma liquida più o meno viscosa. Con l’addizione di additivi indurenti, polimerizzano, assumendo una forma definita. Per questo motivo si chiamano matrici polimeriche termoindurenti.
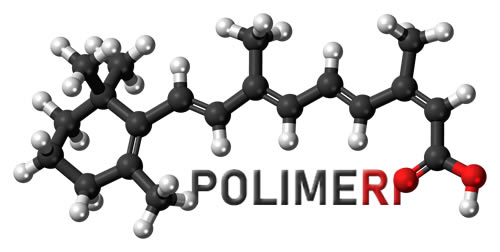
Le tre resine che si utilizzano per la realizzazione della vetroresina sono:
RESINE EPOSSIDICHE: le resine epossidiche sono di colore trasparente ambrato, quasi inodore.Utilizzate in applicazioni critiche, in abbinamento con fibra di vetro, di carbonio e aramidiche. Sono resine dalle alte proprietà adesive, perfette per incollaggi sia di materiali semplici (legno e carta…) che di materiali più duri (acciaio e leghe di alluminio).
- Assicurano ottima resistenza chimica, eccellente resistenza alla corrosione, isolamento elettrico e ottima resistenza meccanica al calore (sono meno soggette a cracking termico).
- Una volta polimerizzate, garantiscono minimo ritiro e buone stabilità dimensionale e comportamento alla fatica.
- I compositi in fibra e resina epossidica assicurano alti valori di resistenza e maggiore è il volume di fibre utilizzate (relativamente a quanto consentito dalla resina epossidica), più alti sono i valori in termini di resistenza e rigidità del composito ottenuto.
- Ideali per prestazioni gravose, ove richiesto un elevato grado di rigidità o forza. Grazie alle loro caratteristiche meccaniche, le resine epossidiche sono ampiamente utilizzate nell'industria aerospaziale.
RESINE POLIESTERE: questa resina si presenta come una colata trasparente dal forte odore dato dalla presenza dallo stirene. Sono le resine più economiche, ma si dimostrano sempre affidabili negli impieghi più comuni.
- Buona resistenza meccanica e chimica, discreta proprietà elettriche e buona stabilità dimensionale.
- Le resine in poliestere trovano applicazione nel settore edile nella produzione di serramenti, condotte e paratie, casseforme e vetrate. Nel settore industriale, per la produzione di componenti di veicoli e mezzi di trasporto, nella costruzione di imbarcazioni. Grazie alle loro elevate proprietà di penetrazione, le resine poliestere sono particolarmente adatte per l’incollaggio con le fibre di vetro. Una volta induriti, i pezzi sono particolarmente resistenti alle intemperie ed all’acqua. Per questo motivo spesso vengono utilizzate per costruire oggetti resistenti agli agenti atmosferici, utilizzate quale sigillante per piscine e vasche e in particolare nel settore nautico nella realizzazione degli scafi da diporto. Inoltre resistono discretamente agli acidi diluiti, non ossidanti e alle soluzioni saline acquose.
- La resina poliestere è adatta anche per la riparazione di parti in plastica e nella realizzazione di oggetti decorativi (bigiotteria, fermacarte, incapsulamenti…), nel modellismo e nella realizzazione di piani di tavolo eleganti.
RESINE VINILESTERE: in termini di qualità di applicazione le resine vinilestere sono una via di mezzo tra le resine epossidiche e quelle poliestere. Garantiscono sempre elevate prestazioni.
- Ottime proprietà meccaniche paragonabili a quelle delle resine epossidiche, elevata resistenza all’idrolisi, eccellente resistenza chimica ed alle alte temperature (fino ai 200°C), ottima resistenza all’abrasione e shock termici.
- La resina vinilestere assicura un’ottima resistenza ai raggi UV, eccellente resistenza all'acqua, ai solventi organici e agli alcali.
- Grazie all’ottima resistenza agli ambienti difficili, la resina vinilestere è ideale per applicazioni nel settore nautico (nella realizzazione di scafi e come barriera anti osmosi) e nel settore industriale nella realizzazione di rivestimenti che devono avere caratteristiche antiritiro e che siano in grado di offrire una protezione superiore alla corrosione e all’aggressione chimica contro acidi ad elevata concentrazione, alcali e solventi aggressivi e calore estremo.
- La facilità di applicazione, (anche su superfici verticali, in quanto non cola) e l’eccellente adesione alle fibre di rinforzo la rendono facilmente abbinabile sia alle fibre di vetro che a quelle di carbonio e aramidica.
Per queste sue caratteristiche (simili ad una epossidica) e per la facilità di utilizzo (simile ad una resina poliestere), la resina vinilestere si posiziona come la soluzione migliore per ottenere un composito sia rigido, che resistente agli ambienti difficili.
Resina epossidica, resina poliestere e resina vinilestere a confronto
Proprietà | Resine epossidiche | Resine poliestere | Resine vinilestere |
Prorpietà adesive |
eccellenti |
nessuna adesività |
buone |
Proprietà termiche chimiche e meccaniche |
eccellenti |
buone |
ottime |
Resistenza agli acidi e aggressivi chimici |
eccellenti |
ottime |
buone |
Resistenza soluzioni saline e acquose - temperatura e umidità |
eccellenti |
ottime |
ottime |
Resistenza alla degradazione UV |
suscettibile (richiede aggiunta di assorbitori dei raggi ultravioletti) |
suscettibile (richiede aggiunta di assorbitori dei raggi ultravioletti) |
ottima |
Resistenza agli urti |
ottima |
discreta |
buona |
Superficie di lavoro |
tutte le superfici |
solo superfici ruvide |
tutte le superfici (anche verticali - non cola) |
Tempo di lavorazione |
rapido (ma precisione nel dosaggio) |
finestra temporale più lunga (dosaggio flessibile in più tempi) |
rapido (ma precisione nel dosaggio) |
Facilità di lavorazione |
media/alta |
facile |
media |
Durabilità ambientale |
eccellente |
buono |
ottimo |
Odore |
scarso o nullo |
pungente (stirene) |
pungente (stirene) |
Restringimento alla polimerizzazione |
basso |
alto |
medio |
Tolleranza allo stretching (stress cracking) |
buona |
media |
buona |
Peso del manufatto finito |
leggero |
medio |
medio |
Tossicità |
medio bassa (lavorabile anche in ambienti chiusi) |
medio alta (stirene: lavorabile all’aperto) |
medio alta (stirene: lavorabile all’aperto) |
Costo materiale |
alto |
medio |
medio |
Rapporto qualità prezzo |
buono |
discreto |
ottimo |
Epossidica, poliestere e vinilestere: quale resina scegliere?
Confrontando le tre resine si può concludere che in considerazione delle caratteristiche meccaniche e chimiche, rigidità finale, resistenza ed il minimo ritiro una volta asciutta e la bassa tossicità per via dell’assenza di stirene, la resina epossidica si pone come la resina migliore.
La resina epossidica è la resina che assicura normalmente i migliori risultati. La meno qualitativa è la resina poliestere mentre la vinilestere è quella che si pone tra le due.
Nei compositi in vinilestere per ottenere prestazioni meccaniche simili ai composti di matrice epossidica, è necessario aumentare di molto la quantità di resina impiegata oltre che la quantità dei rinforzi in fibra a discapito del peso totale del composito. A conti fatti i manufatti in resina poliestere e vinilestere hanno costi di poco inferiori rispetto ai compositi in resina epossidica. Questo perché seppur il costo specifico della resina epossidica sia maggiore, la quantità di materiale utilizzata per la sua produzione è minore. Nonostante ciò e seppur la resina vinilestere sia di qualità media, rimane la più impiegata per via del miglior rapporto qualità prezzo.
Per chi non è un professionista, la resina poliestere che è più facile da miscelare, può essere la soluzione più indicata. Essendo inoltre più economica potrebbe essere vantaggiosa nella valutazione del costo finale, in particolare se servono grandi quantità. Anche il tempo di lavorazione della resina poliestere viene incontro all’utente. È possibile scegliere una diversa finestra temporale fino all’ottenimento dell’indurimento del manufatto, aggiungendo un po’ per volta la quantità di indurente alla resina liquida. Questo non è possibile con la resina epossidica, che richiede una precisa e attenta valutazione della percentuale dei componenti sin dall’inizio, pena la non polimerizzazione o l’ottenimento di un materiale composito molto fragile.
L’innovazione delle resine bio: ecosostenibili ed ecologiche
Negli ultimi anni grazie alla continua ricerca ed allo sviluppo di nuovi materiali eco ambientali si è dato l’avvio alla produzione di una nuova concezione di resina, in linea con la richiesta del mercato bio sostenibile a tutela dell’ambiente. Queste nuove resine Bio vengono prodotte tramite la trasformazione di Biomasse, limitando al massimo l’uso di fonti petrolchimiche. In termini di applicazioni e certificazioni Bio, è stato dimostrato che le resine ottenute non differiscono dalle resine epossidiche tradizionali. Oltre alle resine epossidiche Bio, alcune aziende stanno sperimentando la produzione di resine completamente naturali: partendo da materie prime a base organica vegetale (soia ed estratti lignei di glicerina), mirano ad ottenere resine naturalmente polimerizzanti. Al momento attuale, queste nuove resine “green” assicurano performance limitate, ma nel prossimo futuro, grazie alla continua ricerca saranno senz’altro in grado di allinearsi alle prestazioni delle resine polimeriche “tradizionali”.