1 - INTRODUZIONE
La saldatura è largamente utilizzata in aziende industriali e artigiane per gli evidenti vantaggi che presenta rispetto agli altri sistemi d’unione.
Ai vantaggi legati alla semplificazione nella progettazione del prodotto e all’economicità d’esecuzione, il processo di saldatura contrappone il rischio d’eventi lesivi dell’integrità fisica dei lavoratori addetti e di situazioni d’emergenza nell’ambiente di lavoro generalmente, soprattutto in caso d’inosservanza delle cautele e delle misure di sicurezza previste dalle leggi, regole tecniche e/o norme.
L’ampia diffusione di questo processo tecnologico in aziende piccole, medie e grandi, mirato alla produzione e/o manutenzione, comporta necessariamente un numero d’addetti molto consistente, direttamente esposti ai rischi specifici.
Sono altresì numerose le circostanze, le occasioni ed i momenti che possono generare le emergenze e le situazioni critiche, che scaturiscono dall’uso continuo di gas infiammabili o fonti di calore ad alta temperatura.
Prescindendo, per il momento, dall’analisi del rischio d’eventi dannosi e dalla gravità dei danni prodotti in tali circostanze, riteniamo che, in questa sede, sia giustificata un’attenta riflessione sugli aspetti di questo importante processo, riferiti alla sicurezza ed alla salute degli operatori e di tutti coloro che operano negli ambienti interessati.
Per le sue caratteristiche di pericolosità e d’insalubrità, la saldatura è stata inserita al punto 36 della II parte dell’allegato 1 al Decreto Legislativo (D.Lgs.) 4 agosto 1999, n. 345. Dunque queste attività rientrano tra i processi ai quali è vietato adibire gli adolescenti, ai sensi dell’art. 6 del citato decreto.
La saldatura è stata inoltre inserita nell’elenco delle attività soggette alle visite di prevenzione incendi, di cui al Decreto Ministeriale (DM) 16 febbraio 1982. I rischi connessi alle operazioni di saldatura e all’uso delle relative attrezzature, sono disciplinati da numerose norme di legge, che citeremo puntualmente.
La Costituzione della Repubblica riconosce la tutela della salute e dell’integrità fisica come fondamentale interesse della collettività. Essa attribuisce al diritto alla salute la priorità sulla libertà d’iniziativa imprenditoriale ed economica.
La legge ordinaria ha recepito tali principi ed anche le direttive dell’Unione Europea.
Il dovere di garantire la sicurezza, posto a carico dell’imprenditore, non si esaurisce nell’osservanza della legislazione vigente in materia. In virtù di un principio più generale, all’imprenditore è richiesta una diligenza qualificata nell’adempimento delle sue obbligazioni (art. 1176 del C.C.), fin dalla fase di progettazione delle attività aziendali, per prevedere i rischi, cui saranno esposti i propri dipendenti. In questa analisi dev’essere considerata la particolarità del lavoro, l’esperienza e la conoscenza tecnica, intesa come progresso tecnologico (art. 2087 C.C.), per meglio tutelare l’integrità fisica dei lavoratori.
Il dovere di sicurezza richiesto all’impren-ditore è automaticamente esteso a tutti i possibili rischi, cui sono effettivamente esposti i propri dipendenti. La maggiore ampiezza dell’area dei rischi esistenti rispetto all’area dei rischi disciplinati dalla legislazione, in virtù dei criteri indicati dall’art. 2087 C.C., giustifica l’applicazione delle regole o norme tecniche nei casi concreti, dov’è opportuno integrare una legge generica priva d’indicazioni operative.
Nell'ambito delle limitazioni e dei vincoli posti dalla legge, l’imprenditore ha il diritto d’esercitare il potere organizzativo in qualità di capo dell’impresa (Art. 2086 C.C.). L’imprenditore ha quindi il diritto di pretendere la corretta esecuzione del lavoro da parte dei propri dipendenti, dopo aver osservato tutte le misure generali di tutela e aver adottato tutte le misure di sicurezza specifiche.
A questo diritto dell’imprenditore, corrisponde l’obbligo per i collaboratori inseriti nell’azienda d’operare con la diligenza richiesta dalla natura della prestazione (Art. 2104 C.C.), purché siano stati opportunamente informati, formati, consultati e adeguatamente istruiti.
2- LIMITI DEL CAMPO D’INDAGINE
Anche se la sicurezza degli addetti alla saldatura dipende dall’adeguatezza delle strutture e dell’impiantistica generale dell’unità produttiva, in questa sede non è possibile estendere l’analisi ai rischi generici dell’ambiente, che non siano connessi con lo svolgimento dei compiti specifici di saldatura.
Non tratteremo quindi le problematiche collegate ai rischi relativi ai mezzi di sollevamento e trasporto, alle macchine, agli impianti elettrici generali e agli agenti fisici, chimici e biologici che non siano strettamente attinenti alla saldatura.
Non analizzeremo i parametri ambientali che definiscono il rischio generale, rischio che è diverso da un’unità produttiva ad un’altra, ancorché operanti nello stesso settore merceologico.
Procederemo, quindi, ad un’astrazione, isolando il posto di saldatura dal contesto e limitando l’analisi alle relazioni uomo - macchina - processo.
Considerando la variabilità delle mansioni e dei compiti dei saldatori, nonché la molteplicità delle attrezzature e dei processi, certamente dovremo trascurare alcuni aspetti, peraltro importanti ai fini dell’esame dei rischi esistenti in determinati ambienti.
Il nostro obiettivo è quello d’esaminare i pericoli ed i rischi tipici da controllare ed ottimizzare il grado d’approfondimento, tenendo conto dello spazio assegnato.
3 - OPERAZIONI PRESE IN ESAME
Delle seguenti operazioni:
• saldatura elettrica ad arco con elettrodo rivestito;
• saldatura elettrica ad arco con filo continuo;
• saldatura ossiacetilenica e ossitaglio,
saranno presi in esame soltanto gli aspetti relativi alla prevenzione ed alla protezione, tralasciando le implicazioni tecnologiche e metallurgiche.
4 - SALDATURA ELETTRICA AD ARCO CON ELETTRODO RIVESTITO
Per le caratteristiche delle macchine, delle attrezzature e dei materiali utilizzati e per le peculiarità del processo, in queste operazioni s’identificano molteplici elementi che possiamo definire pericolosi, per loro essenza e natura. Questi elementi, da soli o in concorso con altri, hanno la capacità potenziale di causare danni.
Nell’esercizio normale di quest’attività gli elementi pericolosi hanno una ragionevole probabilità di raggiungere il livello potenziale di danno e quindi costituiscono rischi che devono essere valutati (art. 4, comma 1 del D.Lgs. 19 settembre 1994, n. 626), previsti durante la programmazione della prevenzione (art. 3, comma 1, lettera d), ridotti alla fonte (art. 3, comma 1, lettera d) ed eliminati in base alle conoscenze acquisite dalla tecnica o ridotti al minimo (art. 3, comma 1, lettera b).
Nella fattispecie i rischi specifici sono:
• l’inalazione di polveri, fumi e gas;
• l’esposizione alla radiazione ottica;
• il danno a parti del corpo esposte al calore o proiezioni;
• il rischio proveniente da saldatrici, smerigliatrici ed altre attrezzature;
• il rischio da movimentazione manuale dei carichi.
4.1 - Inalazione di polveri, fumi e gas
Nella saldatura elettrica ad arco, il calore necessario per la fusione dell’elettrodo rivestito e dei lembi degli elementi da saldare è fornito dall’arco voltaico, che raggiunge temperature dell’ordine d’alcune migliaia di gradi centigradi.
L’anima metallica dell’elettrodo, fondendo, fornisce il metallo d’apporto, mentre il rivestimento stabilizza l’arco, protegge il bagno fuso dall’azione dell’atmosfera, lo disossida e dà luogo alla produzione della scoria che lo libera dalle impurità.
I comuni elettrodi hanno l’anima d’acciaio al carbonio, mentre il rivestimento è costituito da polveri sinterizzate a base silice e carbonato di calcio più ossidi di ferro, manganese, titanio, alluminio, ecc.
L’alta temperatura fonde i metalli base e d’apporto e ne trasforma una parte in vapore. Per effetto del successivo raffreddamento, dal vapore si formano particelle solide, che disperse nell’aria circostante e nei gas prodotti dal processo, danno luogo al fumo di saldatura.
Durante la saldatura, la temperatura elevata favorisce la reazione tra azoto ed ossigeno dell’aria, con formazione d’ossidi d’azoto, che, in presenza d’umidità, generano miscele gassose acide.
Si forma anche ossido di carbonio ed un particolato inalabile, le cui particelle contengono:
• manganese;
• nichel;
• cobalto;
• cromo trivalente ed esavalente;
• composti solidi vari.
Alle sostanze sopra indicate si sommano generalmente le polveri prodotte dalla molatura, eseguita sulla cianfrinatura o sul cordone di saldatura.
Tutte queste sostanze sono nocive. Pertanto, nei processi in cui si sviluppano e tendono ad accumularsi, occorre applicare le tecniche di prevenzione e di protezione atte ad evitarne l’inalazione da parte dei lavoratori.
Per prima cosa bisognerebbe eliminare totalmente il rischio. Tuttavia, qualunque cautela si adotti e qualunque materiale o attrezzatura si utilizzi, non è possibile evitare lo sviluppo di polveri e gas nocivi durante il processo di saldatura, così com’è oggi tecnologicamente concepito.
In alternativa all’eliminazione totale del rischio, si deve optare per la sua riduzione al minimo, dopo aver sostituito ciò che è pericoloso con ciò che lo è di meno (art. 3, comma 1, lettera e del D.Lgs. 626/94).
Nella scheda di sicurezza degli elettrodi generalmente utilizzati, si raccomanda di non superare 3.5 mg/m3 per la concentrazione delle polveri nei fumi. Per alcuni elettrodi che sviluppano sostanze più pericolose, detta concentrazione è ridotta a 0.5 mg/m3.
Per la valutazione dei rischi dovuti agli agenti chimici, bisogna far riferimento ai valori limiti di soglia delle concentrazioni degli inquinanti.
In mancanza di una legge in materia, si possono considerare i dati dell’AMERICAN CONFERENCE OF GOVERNAMENTAL INDUSTRIAL HYGIENIST (ACGIH), che dal 1997 consiglia i seguenti limiti di soglia, ossia le concentrazioni degli inquinanti accettabili per una giornata lavorativa di 8 ore, per le sostanze che si sviluppano durante la saldatura:
• manganese 0.2 mg/m3;
• nichel 0.2 mg/m3;
• cobalto 0.02 mg/m3;
• cromo III 0.5 mg/m3;
• cromo VI 0.05 mg/m3;
• ossido di carbonio 29 mg/m3;
• biossido d’azoto 5.6 mg/m3;
• fumi di saldatura 5 mg/m3;
• particelle inalabili 10 mg/m3.
In queste condizioni sorge l’obbligo per il datore di lavoro d’adottare i provvedimenti atti ad impedire o a ridurre, per quanto possibile, lo sviluppo e la diffusione delle polveri, fumi e gas che si sviluppano durante l’operazione di saldatura (art. 20, comma 1 del DPR 19 marzo 1956, n° 303).
Tali provvedimenti consistono nell’aspirazione localizzata degli inquinanti, per quanto è possibile, immediatamente vicino al luogo dove si producono (art. 20, comma 2 del DPR 303/56).
Per consentire di porre la cappa d’aspirazione nella posizione ottimale, in modo che le sostanze nocive che si sviluppano durante la saldatura siano aspirate nella maggior quantità possibile, senza interessare l’ambito respiratorio degli addetti, è consigliabile l’uso di bracci mobili bilanciati, senza i quali, in alcune circostanze, risulta difficile posizionare la cappa d’aspirazione o risulta arduo mantenere la cappa nella posizione di massima efficienza.
Queste attrezzature possono essere d’aiuto per progettare posti fissi di saldatura conformi all’art. 3, comma 1, lettera f del D.Lgs. 626/94, con cui il legislatore dispone il rispetto dei principi ergonomici.
Nonostante l’adozione di tutte le cautele, è possibile che parte dei gas, polveri e fumi si diffondano nell’ambiente e siano inalati, creando problemi alle vie respiratorie dei lavoratori esposti.
La legge prevede la sorveglianza sanitaria, per i lavoratori esposti al rischio d’inalare gli inquinanti in argomento. L’art. 16 del D.Lgs. 626/94, prevede che la sorveglianza sanitaria sia effettuata nei casi stabiliti dalle leggi vigenti, che nel caso specifico sono l’art. 33 del DPR 303/56 e dal punto 19, lettera f della TABELLA DELLE LAVORAZIONI PER LE QUALI VIGE L’OBBLIGO DELLE VISITE MEDICHE PREVENTIVE E PERIODICHE, allegata al DPR 303/56.
Per i saldatori che possono inalare gas nitrosi ed acido nitrico, che si formano a seguito dalla reazione tra l’azoto e l’ossigeno, è prevista una visita medica preventiva e una visita medica trimestrale.
4.1.1 - Dispositivi di protezione individuale
A seguito dell’applicazione di un idoneo impianto d’aspirazione, l’imprenditore può affermare d’aver osservato il principio di protezione sancito dall’art. 3, comma 1, lettera g del D.Lgs. 626/94, che dispone la priorità delle misure di protezione collettive rispetto alle misure di protezione individuali.
Nel nostro caso, ancorché l’imprenditore abbia ipotizzato l’installazione di un idoneo impianto d’aspirazione, non può affermare d’aver eliminato del tutto il rischio d’inalare le sostanze nocive che si sviluppano dalla saldatura. Deve quindi integrare la protezione dei lavoratori esposti al rischio, con idonei dispositivi di protezione individuali (art. 41 del D.Lgs. 626/94), non essendo stato possibile ricondurre sotto la soglia d’accettabilità i rischi residui dopo l’adozione delle possibili misure di sicurezza collettive.
I dispositivi di protezione individuali (DPI) devono essere adeguati alle effettive condizioni del luogo di lavoro e devono tenere conto delle esigenze ergonomiche (art. 42 del D.Lgs. 626/94).
Il datore di lavoro, sulla base della valutazione dei rischi e tenuto conto delle caratteristiche dei DPI esistenti sul mercato, sceglie i più adatti e li mantiene in efficienza. Sul datore di lavoro incombe l’obbligo di fornire adeguate istruzioni ai lavoratori, per l’uso corretto dei DPI.
Il DPI da fornire al lavoratore esposto allo scopo di proteggerne l’apparato respiratorio, dev’essere un respiratore appropriato in relazione alle condizioni dell’ambiente di lavoro.
Per realizzare un programma efficace per la protezione delle vie respiratorie occorre esaminare i seguenti aspetti:
• identificare le sostanze nocive esistenti nell’ambiente e misurarne la relativa concentrazione;
• illustrare chiaramente i lavoratori interessati gli effetti dell’inquinante sulla salute, per renderli consapevoli del rischio cui sono esposti;
• selezionare, tra i dispositivi di protezione delle vie respiratorie esistenti in commercio, quelli che sono specifici per gli inquinanti presenti nell’ambiente e per le concentrazioni rilevate (tutti sanno che una maschera realizzata per proteggere dalle polveri non risulta efficace per gas, vapori e nebbie);
• addestrare il personale all’uso del respiratore, effettuando prove pratiche di tenuta dopo averlo correttamente indossato.
4.2 - Emissioni in atmosfera
Le polveri, i gas e i fumi che si sviluppano durante la saldatura sono aspirati per evitarne la diffusione nell’ambiente di lavoro. Generalmente l’aria aspirata, contenente le polveri, i gas e i fumi, è espulsa in atmosfera, salvo casi particolari, in cui è filtrata e riciclata.
Le emissioni in atmosfera devono essere autorizzate dalle autorità competenti. Nel caso specifico le attività di saldatura d’oggetti e superfici metalliche sono state inserite in quelle a ridotto inquinamento atmosferico, in particolare al punto 30 dell’allegato 2 al DPR 25 luglio 1991.
Ai sensi dell’art. 4 e in applicazione dell’art. 5 dello stesso DPR, la Regione Lombardia ha emesso la Deliberazione della Giunta Regionale n. 6/29881 in data 15/07/1997. Con tale provvedimento, ha dettato i criteri e le procedure per concedere l’autorizzazione in via generale alla costruzione di nuovi impianti od alla modifica sostanziale d’impianti esistenti. Tale autorizzazione assumerà efficacia dal quarantacinquesimo giorno decorrente dal ricevimento della domanda da parte della Regione e del Comune interessato.
Sarà adottata la procedura di cui all’art. 7 del DPR 24 maggio 1988, n. 203, nel caso in cui il Sindaco del comune dovesse esprimere entro il termine di 45 gg, osservazioni di carattere urbanistico - ambientale.
L’autorizzazione in via generale è subordinata alla circostanza che le polveri totali non eccedano la concentrazione di 10 mg/m3 e che la somma degli ossidi di CrVI, Co, Ni, e Cd non superi 1 mg/m3.
Entro 15 giorni dalla data di messa a regime od entro un termine massimo di 105 giorni dall’entrata in esercizio dell’impianto, è necessario presentare i referti analitici relativi alle emissioni alla Regione, al Comune e al Presidio Multizonale d’Igiene e Prevenzione (PMIP), competente per territorio.
La Regione Lombardia, con Deliberazione della Giunta Regionale del 12 febbraio 1999, n. 6/41406, ha confermato che per gli impianti utilizzati per l’esercizio d’attività a ridotto inquinamento atmosferico, le analisi periodiche delle emissioni in atmosfera devono essere effettuate ogni due anni.
Mentre la Regione Lombardia, per gli impianti di saldatura concede l’autorizzazione in via generale all’emissione in atmosfera alle sole condizioni sopra indicate, la Regione Emilia Romagna discrimina le procedure con riferimento all’utilizzo di più di 40 kg di filo il mese. In tal caso applica il criterio del COMITATO REGIONALE INQUINAMENTO ATMOSFERICO EMILIA ROMAGNA n 4.13.19, concedendo l’autorizzazione all’emissione alle seguenti condizioni:
• uso dei metodi UNICHIM per il controllo del rispetto dei limiti d’emissione per polveri, CO e NO2;
• durata dei tre campionamenti, rispettivamente di 60, 60 e 30 minuti;
• volume degli aeriformi prelevati nei tre campionamenti non inferiore a 0.5, 0.5 e 0.006 m3 rispettivamente;
• rispetto dei limiti d’emissione;
• frequenza almeno annuale dei controlli.
Per gli impianti che utilizzano meno di 40 kg di filo il mese, non sono previsti limiti di sostanze inquinanti in emissione. E’ richiesta solamente la tenuta di un registro per l’annotazione dei consumi mensili di materie prime, consumi che risultano dalle relative fatture d’acquisto. Quindi, in Emilia Romagna, il non superamento della soglia dei 40 kg/mese nel consumo di filo rappresenta una semplificazione notevole nella gestione dell’autorizzazione all’emissione in atmosfera.
4.3 - Rischio d’esposizione alla radiazione ottica
L’arco voltaico, oltre al calore necessario a determinare la fusione dei lembi del materiale da saldare, produce una radiazione ottica costituita da:
• radiazione infrarossa;
• radiazione visibile;
• radiazione ultravioletta.
Nel campo delle radiazioni ultraviolette (lunghezza d’onda 400 ÷ 100 nm), esiste un intervallo (320 ÷ 280 nm) detto regione eritemale, per la capacità di provocare arrossamenti della cute.
Le radiazioni emesse dall’arco voltaico interagiscono con la pelle e con l’occhio del lavoratore esposto, dando luogo ad una serie d’effetti negativi, quali:
• bruciori alla pelle e danni alla cornea (radiazione infrarossa);
• iriti e blefariti dell’occhio (radiazione visibile);
• bruciori alla pelle, danni alla cornea ed incremento del rischio stocastico per tumori alla pelle, con effetti a breve e lungo termine (radiazione ultravioletta).
L’entità del danno può dipendere dalla sensibilità individuale del singolo lavoratore a questo tipo di radiazione.
Anche per l’esposizione alle radiazioni ultraviolette l’ACGIH ha proposto valori limiti di soglia, con riferimento alla lunghezza d’onda della radiazione, all’intensità della sorgente ed alla distanza dell’operatore.
A fronte di questi rischi, per la tutela dell’integrità fisica dei lavoratori esposti alla radiazione ottica, la normativa vigente prevede i seguenti obblighi:
• Art. 22 del DPR 303/56. Quando non sia possibile attuare sistemi d’isolamento dell’elemento pericoloso o altre misure collettive di protezione, il datore di lavoro deve provvedere a dotare i lavoratori esposti d’idonei DPI, con particolare riferimento alla protezione degli occhi.
• Art. 19 del DPR 303/56. Per non esporre senza necessità altri lavoratori al rischio, il datore di lavoro deve disporre l’effettuazione delle lavorazioni pericolose possibilmente in luoghi separati. Tale disposizione ha carattere generale e riguarda ogni tipo di rischio, compreso quello prodotto dalla luce viva dell’arco voltaico.
• Art. 259 del DPR 547/55. Obbligo dell’uso di schermi d’intercettazione delle radiazioni nocive, nel caso specifico della presenza nello stesso ambiente di lavoro d’altri lavoratori non addetti alla saldatura, ma esposti comunque al rischio della luce viva dell’arco voltaico.
Gli schermi d’intercettazione devono circondare completamente il posto di saldatura, per bloccare le radiazioni, che, in questo modo non possono raggiungere gli altri lavoratori non interessati alla saldatura. Essi isolano completamente il saldatore. Poiché dall’isolamento totale possono scaturire altri problemi di sicurezza, si usano sempre più frequentemente tende speciali a strisce in grado di conciliare la completa intercettazione delle radiazioni con la visibilità del saldatore al suo posto di lavoro.
4.3.1 - Dispositivi di protezione individuale
Con riferimento al rischio prodotto dalla radiazione ottica emessa dall’arco voltaico, i DPI devono assorbire o riflettere la maggior parte dell’energia irradiata nella lunghezza d’onda nociva, senza alterare in modo eccessivo la trasmissione dalla parte non nociva dello spettro visibile, garantendo la percezione visiva necessaria per operare in sicurezza.
Le lenti non devono deteriorarsi o perdere le loro proprietà per effetto della distanza dalla sorgente.
Sulle caratteristiche di dettaglio dei mezzi di protezione degli occhi, si rinvia alle numerose norme in vigore (per esempio le UNI EN 167, UNI EN 168, UNI EN 169, UNI EN 170 e UNI EN 171).
All’aumentare dell’intensità di corrente assorbita dall’arco voltaico, aumenta l’intensità delle radiazioni emesse e quindi deve aumentare il grado di protezione per gli occhi del lavoratore.
Nell’ambito della saldatura con elettrodi rivestiti è possibile esprimere il grado di protezione con i numeri di graduazione DIN, riferiti alla sensibilità dei filtri. I valori raccomandati sono:
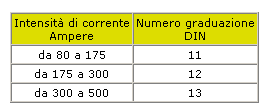
La protezione è oggi possibile anche con filtri opto-elettronici, che possiedono altissime velocità d’oscuramento e capacità di regolazione del grado di protezione DIN in relazione al processo di saldatura, secondo le dichiarazioni dei fabbricanti.
I DPI devono recare impresso il marchio CE, imposto dalla direttiva 89/686/CEE, recepita con D.Lgs. N° 475/92, e devono essere conformi ai requisiti essenziali di sicurezza attestati dal fabbricante. Essi devono limitare il meno possibile il campo visivo e la vista del lavoratore che li utilizza e non devono consentire la penetrazione di polveri, gocce di metallo fuso, vapori, nebbia e fumo. Considerata l’estrema pericolosità dell’esposizione al calore per l’occhio, i DPI devono limitare altresì la penetrazione dell’irraggiamento termico.
Le visiere generalmente collegate ad un elmetto di protezione sono preferibili agli schermi tenuti con le mani dal lavoratore.
L’uso di lenti a contatto durante la saldatura non è consigliabile poiché i fumi ed il particolato potrebbero avere azione irritante sull’occhio. Inoltre, anche se non scientificamente dimostrato, è stato riportato in passato un grave caso di adesione della lente alla cornea di un saldatore.
L’art. 33 del DPR 303/56 obbliga alla sorveglianza sanitaria anche per i rischi alla vista.
In particolare il punto 46 della tabella allegata al DPR 303/56 pone a carico del datore di lavoro l’obbligo della visita medica semestrale, o immediata in caso di segni patologici sospetti, dei lavoratori esposti alle radiazioni ultraviolette ed infrarosse con rischio alla vista.
4.3.2 - Altri indumenti protettivi
Oltre alla protezione dell’apparato respiratorio e degli occhi, il saldatore dev’essere altresì dotato d’altri indumenti protettivi, per proteggere tutte le altre parti del corpo esposte ad altri rischi. I DPI appropriati sono:
• grembiuli di cuoio, per la protezione del tronco (art. 385 del DPR 547/55 e allegato V al D.Lgs. 626/94);
• schermi di protezione per il viso (art. 259 del DPR 547/55 e allegato V al D.Lgs. 626/94);
• guanti isolanti (art. 259 del DPR 547/55) e resistenti all’abrasione, taglio, strappo e perforazione (art. 383 del DPR 547/55 e allegato V del D.Lgs. 626/94);
• scarpe di sicurezza con protezione supplementare della punta del piede per mezzo di puntale d’acciaio ed a slacciamento rapido (art. 384 del DPR 547/55 e allegato V del D.Lgs. 626/94);
•otoprotettori idonei per la protezione dell’udito, perché il saldatore generalmente esegue anche la smerigliatura, che, com’è noto, lo espone a rumore di livello equivalente a circa 100 dB (A). Gli otoprotettori vanno considerati anche con riferimento all’effettivo livello personale giornaliero d’esposizione al rumore (art. 43 del D.Lgs. 15/08/1991 n° 277 ed allegato V del D.Lgs. 626/94);
• tute confezionate con tessuto ignifugo, necessarie per proteggere i saldatori da possibili proiezioni di metallo fuso, scintille o all’esposizione all’alta temperatura dell’arco voltaico (artt. 33 e 378 del DPR 547/55).
4.4 - Saldatrici ed altre attrezzature
Ai sensi dell’art. 35 del D.Lgs. 626/94, il datore di lavoro deve mettere a disposizione dei suoi dipendenti macchine ed attrezzature adeguate alle condizioni ed alle caratteristiche specifiche del lavoro da svolgere, adatte agli scopi da perseguire ed idonee ai fini della sicurezza e della salute, tenuto anche conto degli altri rischi presenti nell’ambiente di lavoro.
Nella scelta delle macchine e delle attrezzature, il datore di lavoro deve orientarsi verso quelle che garantiscono il livello di protezione più elevato, con riferimento all’evoluzione delle tecniche di prevenzione e di protezione (art. 3, comma 1, lettera b del D.Lgs. 626/94).
Considerando i rischi specifici derivanti dall’impiego delle saldatrici, all’atto dell’installazione, che dev’essere eseguita sempre in conformità alle istruzioni fornite dal fabbricante, il datore di lavoro deve collocarle in prossimità d’idonee cappe d’aspirazione dei fumi, gas e polveri, prodotti durante il normale funzionamento (art. 20 del DPR 303/56)
Con particolare riferimento ai rischi elettrici, dev’essere attuata un’idonea manutenzione delle saldatrici, per garantire i necessari requisiti di resistenza e d’idoneità ed il mantenimento in buono stato di conservazione e d’efficienza (art. 374 del DPR 547/55 e art. 36 del D.Lgs. 626/94).
In relazione alle concrete esigenze della sicurezza ed alle peculiarità della singola azienda, il datore di lavoro stabilisce i modi, i tempi e le procedure di manutenzione ed incarica personale qualificato, idoneo allo svolgimento dei suddetti compiti.
Un’altra norma di carattere generale che merita d’essere citata in questa sede, è l’art. 37 del D.Lgs. 626/94, che pone a carico del datore di lavoro l’obbligo d’acquisire tutte le informazioni e le istruzioni d’uso possibili, in relazione alle necessità della sicurezza delle macchine ed attrezzature. Tali istruzioni devono essere trasferite in modo chiaro, efficace e comprensibile ai lavoratori interessati.
4.4.1 - Rischi connessi all’uso delle saldatrici e smerigliatrici e relative misure di sicurezza
È vietato effettuare operazioni di saldatura: su recipienti chiusi; su recipienti contenenti sostanze che possono dar luogo ad esplosione; all’interno di locali, recipienti o fosse, che non siano efficacemente ventilati (art. 250 del DPR 547/55);
Le saldatrici devono essere provviste d’interruttori onnipolari sul circuito primario di derivazione della corrente elettrica (art. 255 del DPR 547/55);
All’interno di recipienti metallici, per l’esecuzione della saldatura elettrica, devono essere predisposte misure tali da impedire contatti accidentali con elementi in tensione. Queste operazioni devono essere eseguite sotto la sorveglianza continua di un esperto, che assista il lavoratore dall’esterno del recipiente (art. 257 del DPR 547/55);
La zona d’operazione della saldatura elettrica ad arco dev’essere protetta con schermi d’intercettazione delle radiazioni dirette e di quelle riflesse, per evitare il pericolo per gli altri lavoratori, che operano in prossimità (art. 259 del DPR 547/55). Per raggiungere l’obiettivo dell’intercettazione totale delle radiazioni, normalmente si segrega completamente la zona di saldatura, isolando il saldatore dalla vista dei colleghi, che operano nell’area circostante. Si determina così l’inconveniente, in caso d’emergenza sanitaria, che il saldatore possa non ricevere un’assistenza tempestiva. In questo caso viene meno il principio di prevenzione per cui la misura di sicurezza dev’essere adeguata al rischio da prevenire, senza tuttavia comportare di per sé un rischio maggiore. Per questo e per altri motivi, si possono, in alternativa ai tradizionali schermi di lamiera, installare delle tende di plastica a strisce, dichiarate autoestiguibili dal fabbricante, che resistono alle proiezioni incandescenti emesse da saldatrici e dalle smerigliatrici (artt. 12 e 75 del DPR 547/55) e filtranti, nel senso che proteggono dalle radiazioni nocive prodotte da qualsiasi tipo di saldatura e per qualsiasi valore dell’intensità di corrente. Ma la caratteristica più importante di queste tende è la trasparenza che consente una visione sia dall’interno sia dall’esterno della postazione di saldatura.
Le saldatrici devono essere alimentate da impianti elettrici costruiti, installati e mantenuti in modo da prevenire i pericoli derivanti da contatti con elementi in tensione ed i rischi d’incendio e di scoppio, derivanti da anomalie di funzionamento (art. 267 del DPR 547/55).
Le saldatrici devono portare per tutto il tempo per il quale sono utilizzate l’indicazione della tensione, dell’intensità e del tipo di corrente, della potenza e delle altre caratteristiche costruttive necessarie per un uso conforme alle norme di sicurezza (art. 269 del DPR 547/55).
I conduttori d’alimentazione delle saldatrici mobili, particolarmente i tratti di conduttore appoggiati sul pavimento e quelli che per la loro posizione siano soggetti a danneggiamento per cause meccaniche (passaggio di carrelli, cadute di pezzi metallici potenzialmente taglienti, ecc.) devono avere il rivestimento isolante protetto in modo specifico anche contro l’usura meccanica (artt. 282 e 283 del DPR 547/55).
I circuiti d’alimentazione delle saldatrici elettriche devono essere provvisti di valvole fusibili o d’interruttori automatici, atti ad impedire la circolazione di correnti d’intensità tali da raggiungere temperature pericolose (art. 285 del DPR 547/55). Le valvole devono essere collocate a valle degli interruttori e consentire il ricambio dei fusibili sotto tensione, senza pericolo per il lavoratore (art. 295 del DPR 547/55).
Considerato che la potenza delle saldatrici supera abbondantemente i 1000 Watt, la derivazione a spina dev’essere provvista a monte della presa d’interruttore in modo da consentire l’inserimento ed il disinserimento della spina a circuito aperto (art. 311 del DPR 547/55). Oggi i quadri elettrici, non solo consentono la cautela di cui sopra, ma non permettono un comportamento che possa trasgredirla.
Le saldatrici mobili e le smerigliatrici portatili possono essere alimentate solo da circuiti a bassa tensione di cui all’art. 268 del DPR 547/55 (art. 312 del DPR 547/55).
Per le operazioni di smerigliatura da effettuare all’aperto è vietato alimentare l’utensile elettrico portatile con tensione superiore ai 220 V.
Nei luoghi bagnati o molto umidi e nei lavori a contatto con grandi masse metalliche, la tensione non dev’essere superiore a 50 V (art. 313 del DPR 547/55):
L’involucro metallico delle saldatrici mobili e delle smerigliatrici portatili dev’essere collegato elettricamente a terra. L’attacco del conduttore di terra dev’essere realizzato, nella spina e nella presa, rispettivamente con spinotto e con alveolo supplementari (art. 314 del DPR 547/55).
Per i collegamenti elettrici a terra devono essere usati conduttori di sezione adeguata all’intensità della corrente verso terra e comunque non inferiori alla sezione dei conduttori del circuito elettrico (art. 324 del DPR 547/55).
I conduttori di "massa" devono avere sezione adeguata ed essere collegati al pezzo da saldare in vicinanza della zona d’operazione.
I conduttori di terra devono essere protetti contro il danneggiamento e il deterioramento e devono essere connessi con sistemi efficienti (art. 325 del DPR 547/55).
L’impianto di messa a terra dev’essere adeguato alle caratteristiche e alle particolarità degli impianti utilizzatori e deve presentare una resistenza che garantisca l’incolumità dei lavoratori (art. 326 del DPR 547/55).
Gli impianti di messa a terra devono essere denunciati all’Azienda Sanitaria Locale (ASL) competente, verificati prima della messa in servizio e periodicamente ad intervalli non superiori a due anni (art. 328 del DPR 547/55).
4.4.2 - Smerigliatrici
Alle smerigliatrici usate per molare i cianfrini ed il cordone di saldatura, s’applicano le norme di sicurezza previste per gli utensili portatili, ossia degli utensili che devono essere sostenuti dallo stesso operatore durante l’uso.
In particolare:
• devono subire un controllo di massima da parte dell’utente prima d’essere usati, per accertarne la conformità alle norme di sicurezza, illustrate ai lavoratori durante la formazione;
• le parti metalliche esterne devono risultare collegate elettricamente a terra;
• devono essere muniti di un interruttore incorporato nell’incastellatura che consente d’eseguire con facilità e sicurezza la messa in moto e l’arresto. E’ necessario che l’azionamento dell’organo di comando d’avviamento e d’arresto sia effettuato senza abbandonare i mezzi di presa e di mantenimento nella posizione di sicurezza. Questi risultati possono essere raggiunti con un interruttore a uomo presente;
• i mezzi di presa e di mantenimento in posizione di sicurezza, devono essere dimensionati e collocati in modo da garantire la stabilità dell’utensile nelle condizioni di funzionamento previste dal fabbricante;
• devono essere dotate del marchio "CE" in ottemperanza alla direttiva macchine 98/37/CE (art. 8);
• devono rendere minimi gli effetti del rumore prodotto;
• devono essere progettate e realizzate in modo da rendere minima la produzione e la trasmissione delle vibrazioni alle mani e al corpo del lavoratore;
• il disco della smerigliatrice dev’essere ben fissato all’albero che lo trascina in rotazione;
• il disco della smerigliatrice dev’essere protetto da una cuffia robusta e idonea ad evitare il contatto accidentale con il disco in rotazione, nella parte non impegnata nell’operazione d’asportazione del truciolo.
4.4.3 - Scalpelli per la rimozione della scoria di saldatura
In quanto utensili portatili hanno le stesse esigenze di presa, mantenimento, azionamento e contenimento degli effetti dei rumori prodotti durante l’uso, già descritti per le smerigliatrici.
Le peculiarità, in termini di sicurezza di questi utensili sono le seguenti:
• sono azionati da aria compressa;
• bisogna controllare l’integrità delle tubazioni flessibili, il pressostato e la valvola di sicurezza sul compressore (art. 167 del DPR 547/55);
• controllare le connessioni, lo scarico dell’aria ed eventuali silenziatori;
• controllare i dispositivi smorzatori delle vibrazioni;
• verificare che l’utensile a contatto della scoria da rimuovere, sia ben fissato all’apparecchio in modo da evitare sfilamenti accidentali;
• accertare che in caso d’uso non occasionale di tali utensili il lavoratore sia sottoposto alla sorveglianza sanitaria per i rumori (art. 59 del D.Lgs. 277/91) e per le vibrazioni (punto 48 della tabella allegata al DPR 303/56).
4.5 - Movimentazione manuale dei carichi nella postazione di saldatura
La movimentazione dei pezzi da saldare sul tavolo di lavoro e degli utensili scalpelli e smerigliatrici per l’esecuzione delle attività complementari alla saldatura, sono operazioni che il saldatore ripete sistematicamente.
Gli utensili portatili normalmente non superano il peso di 5 kg, la lunghezza di 500 mm e l’altezza di 150 mm, mentre i pezzi da saldare possono avere forme e dimensioni le più varie possibili. Dunque non sempre le condizioni ergonomiche, in cui si svolge effettivamente l’attività di saldatura, possono definirsi favorevoli.
L’obbligo del datore di lavoro non è quello d’evitare la movimentazione manuale dei carichi, bensì quello d’evitare la necessità d’una movimentazione manuale dei carichi (art. 48 del D.Lgs. 626 /94), che comprende, oltre al sollevamento, anche la spinta, il traino e il sostegno. Per raggiungere lo scopo, il datore di lavoro deve adottare le misure organizzative idonee e ricorrere a mezzi appropriati.
Qualora non sia possibile evitare la movimentazione manuale dei carichi, il datore di lavoro deve fornire mezzi adeguati allo scopo di ridurre i rischi che essa comporta. A tal fine il posto di lavoro dev’essere organizzato in modo che la movimentazione sia il più possibile sicura con riferimento alle caratteristiche del carico, che sono:
• il peso, nelle condizioni peggiori, non deve superare i 30 kg;
• per il sollevamento occorrono spazi non ristretti;
• il sollevamento dev’essere eseguito con due mani;
• la frizione tra la suola delle scarpe e il pavimento dev’essere adeguata;
• i gesti di sollevamento non devono essere bruschi;
• il carico non dev’essere estremamente caldo o freddo;
• il contenuto del carico dev’essere stabile.
Per evitare i rischi di lesioni dorso lombari, si considerano la distanza orizzontale del carico dal corpo, l’altezza da terra all’inizio del sollevamento, l’altezza alla quale bisogna depositare il carico, la frequenza dei sollevamenti e l’eventuale asimmetria dei gesti.
Questo rischio di per sé comporta l’obbligo della sorveglianza sanitaria (art. 48, comma 4, lettera c del D.Lgs. 626/94), indipendentemente dagli altri rischi cui è esposto il lavoratore. Durante la visita medica, ai fini del giudizio d’idoneità, si devono considerare i fattori individuali di rischio. Questo significa che il lavoratore con problemi dorso lombari d’una certa entità non può essere esposto a rischi normali, ma solo ad alcuni molto controllati.
La formazione e l’informazione, che sono diventati due pilastri della prevenzione da quando l’uomo è stato posto al centro della sicurezza, in materia di movimentazione dei carichi hanno ricevuto una disciplina molto dettagliata. Il datore di lavoro è tenuto a fornire informazione sul carico e sulla sua corretta movimentazione.
5 - SALDATURA AD ARCO ELETTRICO CON FILO CONTINUO
Quest’operazione differisce dalla saldatura con elettrodo rivestito, limitatamente a determinati aspetti del processo, che modificano i rischi sopra esaminati, in termini qualitativi e quantitativi.
Il materiale d’apporto è costituito da un filo continuo non rivestito, che è erogato da una pistola mediante dispositivo di trascinamento.
Il bagno fuso e le zone circostanti sono protetti da un gas, o da una miscela di gas, che fluisce dalla pistola. La possibilità di un’alimentazione continua (esclusa nella saldatura con gli elettrodi rivestiti) espone il lavoratore per più tempo all’azione delle radiazioni emesse dall’arco voltaico, a parità di durata complessiva della prestazione.
Con questo processo, la radiazione, proveniente dall’arco, che investe il lavoratore, è molto più intensa, rispetto a quella prodotta dall’elettrodo rivestito, perché i fumi che si sviluppano sono meno densi e in quantità minore.
In queste circostanze la pelle e l’occhio del lavoratore sono maggiormente sollecitate dalle radiazioni più intense e più prolungate. In relazione al caso concreto potrebbe essere richiesta una sorveglianza sanitaria più frequente ed una maggiore protezione della pelle e soprattutto degli occhi.
A tal fine, le precedenti indicazioni relative alla saldatura ad elettrodo rivestito sul grado di protezione dell’occhio dei vetri inattinici, espresse in numeri di graduazione DIN, riferiti alla sensibilità dei filtri, in funzione dell’intensità di corrente impiegata, devono essere modificate ed adattate al processo a filo continuo, come segue:
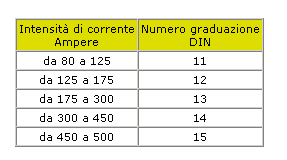
I gas di protezione del bagno per i diversi processi di saldatura sono normalmente i seguenti:
MIG (Metal inert Gas) = gas inerte, principalmente Ar;
MAG (Metal Active Gas) = gas ossidante CO2 o parzialmente ossidante (per esempio la miscela 80 % Ar + 20 % CO2).
E’ opportuno che l’uso di questi gas avvenga in ambienti ampi e ventilati. In ambienti di ridotte dimensioni, l’argon (Ar) e l’anidride carbonica (CO2) potrebbero sostituire l’aria e, oltre un certo limite, renderebbero impossibile la respirazione. La concentrazione minima dell’anidride carbonica che non consente più la respirazione è 15 % circa. Per evitare il rischio d’asfissia, la saldatura MIG e MAG dev’essere eseguita in ambienti di volume adeguato e con una ventilazione, tale da garantire almeno 10 ricambi d’aria/ora.
Un altro pericolo, ancorché poco probabile, è costituito dalla trasformazione dell’anidride carbonica in ossido di carbonio, che sommatosi alle altre fonti potrebbe raggiungere concentrazioni pericolose. Per questo gas, il limite di soglia proposto dal ACGIH è 29 mg/m3.
I lavoratori addetti alla saldatura, esposti al pericolo d’inalare ossido di carbonio, ai sensi del punto 25 della più volte citata tabella delle lavorazioni allegata al DPR 303/56, devono essere sottoposti a visita medica semestrale.
Un’altra peculiarità di questo processo, è la produzione d’ozono, in misura maggiore che non nella saldatura ad elettrodo rivestito. A determinate concentrazioni l’ozono è irritante e molto nocivo.
La determinazione delle concentrazioni di tutte queste sostanze richiede un’accurata indagine ambientale, i cui risultati rappresentano i presupposti per le seguenti valutazioni:
• scelta del respiratore più adatto;
• valutazione dell’efficacia delle misure di sicurezza collettiva;
• elaborazione d’un programma di sorveglianza sanitaria mirato agli inquinanti effettivamente esistenti nell’ambiente.
6 - SALDATURA OSSIACETILENICA E OSSITAGLIO.
Anche se sono operazioni diverse, anzi opposte nei fini, (la saldatura ossiacetilenica è realizzata per unire due pezzi, mentre l’ossitaglio divide un pezzo in più parti), esse hanno in comune i mezzi per la loro esecuzione e presentano rischi analoghi.
Infatti, entrambi i processi utilizzano il calore prodotto dalla combustione dell’acetilene con l’ossigeno, che fluiscono attraverso un dispositivo, detto cannello ossiacetilenico.
La saldatura ossiacetilenica, che fu il primo processo di saldatura impiegato industrialmente, è da anni in declino per motivi di qualità, di produttività e d’economia. L’ossitaglio, invece, è ampiamente usato in carpenteria, nella cantieristica e nella manutenzione.
La combustione dell’ossigeno e dell’acetilene genera la fiamma ossiacetilenica, che presenta due parti nettamente distinte: il dardo, bianco immediatamente all’uscita del foro del cannello, e il fiocco dal contorno ben definito, ma poco luminoso. Il dardo utilizza l’ossigeno proveniente dalla bombola, il fiocco quello presente nell’aria dell’ambiente.
Se la combustione è completa, i prodotti della reazione sono costituiti da anidride carbonica e vapore acqueo. Se la combustione è incompleta per carenza d’ossigeno, si forma anche ossido di carbonio.
Con una regolazione normale, il dardo raggiunge la temperatura di circa 3000 °C.
Per realizzare un taglio termico, utilizzando l’ossitaglio, è necessario prima portare il pezzo d’acciaio al colore bianco, ossia alla temperatura di circa 1300 °C, impiegando la fiamma di riscaldamento. Successivamente si usa l’ossigeno per il taglio. La portata e la velocità del getto d’ossigeno sono funzione dello spessore del pezzo da tagliare e determinanti per ottimizzare la velocità e qualità d’esecuzione del taglio.
L’operazione d’ossitaglio produce notevoli quantità di polveri, peraltro spinte energicamente nella direzione del getto d’ossigeno. Per evitare la diffusione delle polveri e degli altri inquinanti nell’ambiente, le cappe d’aspirazione descritte per la captazione delle polveri prodotte dalla saldatura elettrica ad arco non risultano sufficienti in questo caso. Per l’ossitaglio esse devono esser integrate con vasche d’acqua, che catturano le polveri emesse e non danno loro la possibilità di disperdersi nell’ambiente.
Gli impianti di saldatura e d’ossitaglio acetilenico possono essere fissi o mobili. Nel primo caso, i tubi di gomma d’alimentazione del cannello coi gas combustibile e comburente sono collegati ai rispettivi rubinetti di distribuzione installati nel locale. Nel caso secondo caso, l’alimentazione avviene con tubi di gomma collegati alle bombole, trasportate da appositi carrelli.
I rischi, prodotti dalle operazioni in argomento, sono legati alla pericolosità intrinseca dei due gas utilizzati ed alle modalità operative del processo.
6.1 - Rischi dovuti all’uso d’ossigeno.
L’ossigeno è uno degli elementi più diffusi in natura e costituisce il 21% dell’atmosfera terrestre. Esso è il comburente od ossidante per antonomasia. Per ottenere le grandi quantità di calore nell’unità di tempo e le alte temperature del dardo della fiamma ossiacetilenica, occorre che l’ossigeno, che alimenta il cannello, abbia una concentrazione del 98÷99 %. Con questa concentrazione è fornito in bombole da 50 litri alla pressione di 200 atmosfere. La bombola contenente ossigeno ha l’ogiva di colore bianco. Per impedire la fuoriuscita d’ossigeno dalla bombola durante il trasporto, la stessa dev’essere dotata d’idonea chiusura e protezione, come dispone l’art. 248 del DPR 547/55. Le bombole d’ossigeno e le apparecchiature annesse, dovendo resistere alla pressione di 200 atmosfere, devono possedere i necessari requisiti di resistenza e d’idoneità di cui all’art. 241 del DPR 547/55. L’ossigeno arriva al cannello con una pressione ridotta e costante compatibile con le necessità del processo, mediante un riduttore.
L’ossigeno allo stato gassoso è molto ossidante e reagisce con quasi tutti i metalli e metalloidi. In condizioni normali di temperatura e di pressione, ha un peso specifico di 1,10535 rispetto all’aria. Se liberato in ambienti non ventilati, fa aumentare la velocità di combustione e la temperatura della fiamma, riduce la temperatura d’accensione e l’energia necessaria per l’innesco. In atmosfera arricchita d’ossigeno sono enfatizzate le caratteristiche connesse con l’ossidazione consentendo a scintille ed inneschi normalmente innocui d’accendere materiali anche poco combustibili.
Vi sono pertanto alcune operazioni che vanno evitate o comunque eseguite con molta cautela. Per esempio:
• evitare il contatto tra oli e grassi minerali con il manometro, il riduttore e la valvola della bombola contenente ossigeno;
• non usare fiamme libere per cercare eventuali perdite nelle tubazioni di gomma che collegano il cannello alla bombola;
• non esporre la bombola al sole estivo o ad alte temperature per evitare pericolosi incrementi di pressione;
• il trasporto delle bombole contenenti ossigeno all’interno dei luoghi di lavoro, dev’essere effettuato con mezzi atti ad assicurarne la stabilità ed evitare urti pericolosi (art. 254 del DPR 547/55);
• le bombole in deposito, o che alimentano posti fissi di saldatura, devono essere efficacemente ancorate, per evitarne la caduta (art. 254 del DPR 547/55);
• ventilare all’aria aperta la tuta o altri indumenti che siano saturi d’ossigeno, per esposizione accidentale. L’aumento delle proprietà d’infiammabilità e il contatto accidentale con la fiamma o con particelle calde o incandescenti potrebbero determinare ovvie situazioni di rischio;
• in ambienti ricchi d’ossigeno evitare d’indossare indumenti sintetici che potrebbero dar luogo a cariche elettrostatiche;
• negli ambienti di cui sopra evitare altresì di indossare abiti sporchi d’olio o grasso.
6.2 - Rischi dovuti all’uso dell’acetilene.
L’acetilene è un gas incolore e inodore quando è puro. Quello utilizzato nei processi di saldatura ossiacetilenica è impuro d’H2S (acido solfidrico) e PH3 (fosfina) che gli conferiscono il caratteristico odore agliaceo. Ha una densità di poco inferiore a quella dell’aria per cui se si libera in un ambiente tende a sollevarsi verso l’alto, ma potrebbe anche trovare equilibri diversi. Ha limiti molto ampi d’infiammabilità in aria, compresi tra il 2.4 e 83 % in volume. Per concentrazioni al di sotto del 2.4 %, la quantità d’acetilene non è sufficiente per dar luogo né alla combustione né all’esplosione. Al di sopra della concentrazione dell’83 % in aria, la quantità d’ossigeno presente è insufficiente per attivare combustione o l’esplosione.
Le perdite d’acetilene dalla valvola o dal riduttore possono dar luogo a dardi di fuoco, se s’innesca la fiamma immediatamente. Se l’innesco è ritardato rispetto al momento della fuga e la miscela assume una concentrazione tra i limiti d’infiammabilità è possibile l’esplosione.
Se poi la bombola d’acetilene è investita dalle fiamme, l’aumento di temperatura del corpo della bombola determina un aumento della pressione interna del gas, che sommato alla diminuzione della resistenza meccanica della bombola, può generare lo scoppio. In tal caso si libera un’onda di pressione, con proiezione di frammenti metallici fino a notevoli distanze. Il gas sprigionato forma una sfera di fuoco, nella quale la combustione diventa sempre più violenta, man mano l’aria affluisce all’interno. La combustione e l’incendio si diffondono rapidamente in tutto l’ambiente.
L’uso, il trasporto e il deposito delle bombole d’acetilene costituiscono operazioni importanti ai fini della sicurezza, e, se le quantità in deposito superano i valori indicati nel DM 16 febbraio 1982, è richiesta almeno l’osservanza delle seguenti cautele:
• il locale di deposito dev’essere in muratura;
• il locale non dev’essere interrato (art. 251 del DPR 547/55);
• la porta d’accesso dev’essere incombustibile e apribile verso l’esterno;
• la distanza da altri fabbricati dev’essere almeno 8 m;
• la distanza dalle vie di transito o d’esodo dev’essere almeno 2 m;
• il luogo dev’essere ben ventilato;
• nel locale dev’esser vietato fumare e l’uso delle fiamme o scintille (art. 34 del DPR 547/55);
• nel locale dev’essere impedita la formazione di cariche elettrostatiche;
• le bombole devono essere tenute in posizione verticale anche per evitare l’uscita d’acetone, che potrebbe rendere instabile l’acetilene alla pressione esistente nella bombola (vedi appresso);
• le bombole devono essere tenute al riparo dai raggi solari e da ogni fonte di calore e sempre a temperatura inferiore a 50 °C.
Altre caratteristiche dell’acetilene, rilevanti ai fini della sicurezza sono:
• l’inalazione dell’acetilene in miscela con l’aria ad alta concentrazione, può causare asfissia;
• l’inalazione a bassa concentrazione, può avere effetto narcotico, con nausea e perdita di coordinamento;
• l’acetilene è instabile a pressioni superiori a quella atmosferica. Sfruttando la solubilità dell’acetilene in acetone e la stabilità di tale soluzione anche alla pressione di 12÷15 atmosfere, questo gas è commercializzato in bombole che ne contengono 5 kg alla pressione massima di 15 atmosfere. Per garantire la stabilità, l’acetilene è disciolto in acetone adsorbito in una sostanza porosa che occupa l’intero volume della bombola.
• per evitare l’uscita d’acetone dalla bombola e quindi evitare che sia compromessa la stabilità dell’acetilene, occorre limitare la portata d’acetilene del cannello a meno di 900 litri/ora. Per lo stesso motivo occorre evitare di proseguire nell’alimentazione del cannello quando la bombola si sta esaurendo;
• sulla derivazione dell’acetilene dev’essere inserita una valvola di sicurezza, per impedire il ritorno di fiamma (art. 253 del DPR 547/55).
7 - RISCHIO D’INCENDIO
Tutti i rischi che abbiamo esaminato in precedenza riguardano prevalentemente il saldatore o le persone che operano in prossimità del posto di saldatura. Infatti, le polveri, i fumi, i gas, le radiazioni che si sviluppano dall’arco voltaico, i rischi elettrici, i rischi d’ustione per contatti accidentali con elementi caldi, la movimentazione manuale dei carichi e i rumori prodotti dalla smerigliatrice, restano in un ambito più o meno ristretto. Questo non significa sottovalutarne gli effetti negativi sui lavoratori esposti, ma soltanto circoscriverne l’area di competenza rispetto alla vastità di un eventuale incendio, che finisce per interessare altre aree ed altri lavoratori, anche se nasce nel reparto saldatura.
La premessa che abbiamo fatto, riferita ad altri rischi, vale a maggior ragione per il rischio d’incendio. Di questo rischio non è possibile fare un’analisi generica, perché ogni caso concreto necessita di uno studio approfondito.
Sappiamo che la saldatura costituisce certamente una fonte d’innesco, con la costante emissione di particelle calde ed incandescenti, e che rappresenta un pericolo d’incendio specifico. Non sappiamo invece quali e quanti materiali esistano in un’ipotetica azienda, qual’è la loro attitudine alla combustione, se investiti dal fuoco. Occorrerebbe individuare le quantità dei materiali utilizzati nel ciclo produttivo e quelle in deposito, secondo le seguenti caratteristiche di reazione al fuoco:
• non combustibili;
• autoestinguenti;
• ritardanti la fiamma;
• combustibili normali;
• molto combustibili;
• infiammabili.
Conoscendo le quantità dei materiali, la loro dislocazione, la reazione al fuoco e il rispettivo potere calorifico, si possono determinare le quantità di calore e di fumi prodotti nel tempo e nello spazio, in caso d’incendio, nonostante l’adozione di tutte le possibili misure di sicurezza. Ipotizzando un determinato tipo di sviluppo dell’incendio, si possono calcolare la temperatura raggiunta dalle strutture ed i tempi d’esposizione. Durante la progettazione, Sulla base di questi dati, è possibile definire la resistenza al fuoco che i materiali scelti per le strutture devono avere per contenere il più possibile i danni d’un eventuale incendio.
La resistenza al fuoco è stata definita come l’attitudine dei materiali a conservare, per un tempo stabilito, le seguenti caratteristiche:
• resistenza meccanica (R);
• esposizione al fuoco (E) intesa come attitudine ad impedire il passaggio di fiamme, vapori e gas caldi dal lato opposto a quello investito dal fuoco;
• isolamento termico (I) inteso come attitudine ad impedire il passaggio di calore sul lato non esposto al fuoco.
Per esempio, un materiale che sotto l’azione del fuoco conserva la resistenza meccanica, la tenuta all’esposizione e l’isolamento termico per 120 minuti, ha una resistenza al fuoco che si può indicare con la sigla REI 120.
Partendo dai potenziali sviluppi di calore e di fumi, si progettano le protezioni da adottare, che sono di due tipi:
• protezioni passive, di tipo strutturale (compartimentazioni, porte tagliafuoco, uscite e scale di sicurezza, illuminazione d’emergenza, ecc.);
• protezioni attive, di tipo impiantistico (rete antincendio, sprinkeler automatici, rivelatori di gas, fumo e fiamme, estintori, ecc.).
Vi sono poi provvedimenti di tipo organizzativo, che costituiscono una protezione passiva, come il lay-out che non ostacola la fuga in caso d’emergenza, o la costituzione della squadra d’emergenza, che appartiene alla categoria delle protezioni attive.
8 - AZIONI CORRETTIVE
Durante l’analisi dei rischi, è necessario valutare la probabilità con cui possono accadere gli eventi nocivi per l’integrità e la salute dei lavoratori e le conseguenze, in termini d’entità dei danni.
Dalla matrice di rischio si rivelano le zone a rischio elevato, medio, limitato e trascurabile. Preso atto dei componenti più critici degli impianti e delle fasi più pericolose del processo, s’individuano le azioni correttive atte a consentire una significativa riduzione della probabilità di danno. In particolare si definiscono gli intervalli d’ispezione ritenuti congrui con i vari livelli di rischio. Realizzando interventi mirati d’ispezione e di manutenzione sulle situazioni critiche, si ottengono benefici sia in termini d’elevati livelli d’affidabilità degli impianti e dei mezzi di lavoro, sia benefici relativi alla riduzione dei costi.
Per raggiungere il risultato di una distribuzione ottimale delle risorse nella definizione dei programmi ispettivi, occorre, oltre alla conoscenza generale sui rischi, anche una specifica esperienza di quel determinato ambiente. Un esame periodico del registro degli infortuni consente di tenere meglio sotto controllo i pericoli che hanno già manifestato la loro potenzialità.
9 - CONCLUSIONI
Tenendo conto dello spazio disponibile, non è stato possibile affrontare altri argomenti collegati alle problematiche trattate, né si è ritenuto opportuno approfondire ulteriormente alcuni aspetti a danno di altri. In questo, come in altri campi, lo sviluppo ottimale di più argomenti vasti, in spazi limitati, ha sempre un margine d’opinabilità.
Noi riteniamo, sulla base d’esperienze acquisite in attività di vigilanza sull’osservanza di queste norme, nella direzione di alcune funzioni aziendali, nella consulenza e nella attività progettuale di piani formativi, d’avere acquisito una visione globale delle problematiche di prevenzione e protezione, che ci consente d’offrire spunti ed idee per l’analisi e la valutazione dei rischi.
Nota: By: AQM