Per consentire l'unione tra due metalli mediante saldatura occorre quasi sempre raggiungere temperature molto elevate. La fonte di calore utilizzata caratterizza il tipo di procedimento impiegato (es.: saldatura con gas, saldatura ad arco).
Uno dei più importanti problemi da risolvere durante la saldatura è che, con l'aumento della temperatura, aumenta anche la propensione dei metalli a combinarsi con l'atmosfera.
Il mezzo con cui si protegge il metallo fuso dall'attacco atmosferico è la seconda caratteristica che distingue i vari processi.
Vengono pertanto distinte le tecniche che prevedono l'impiego di polveri che producono della scoria, oppure gas di protezione inerti. In alcuni casi però , l'atmosfera viene del tutto eliminata creando degli ambienti sottovuoto.
Alcuni procedimenti ..
Alcuni procedimenti sono stati sviluppati per l'impiego in campi di applicazione specifici mentre altri rivestono carattere di utilizzo più generale. Sebbene la saldatura sia generalmente riferita all'unione di due metalli simili e persino dissimili fra loro, si utilizza saldatura anche per riparare o ricostruire parti metalliche usurate o danneggiate. Un altro campo di applicazione di crescente interesse è quello della "ricarica" di nuovi componenti al fine di migliorarne la resistenza alla corrosione, all'abrasione, agli urti o all'usura. In questi ultimi casi si deposita uno o più strati di materiale d'apporto su un componente avente un basso costo o un carico di rottura più elevato. Inventato agli inizi del 19.mo secolo, il procedimento di saldatura ad arco è ancora ai giorni nostri il metodo più utilizzato. Come suggerisce il nome stesso , il calore necessario per fondere si ottiene da un arco elettrico che si origina tra il pezzo da saldare e il metallo d'apporto. L'energia elettrica che viene convertita in calore genera una temperatura d'arco di circa 7000°C che fonde i metalli da unire. Gli impianti impiegati possono essere diversi sia in dimensione sia in complessità e ,a secondo del procedimento di saldatura impiegato per proteggere il bagno di fusione, prendono il nome dal materiale d'apporto utilizzato. I procedimenti ad arco si dividono in:
1] ELETTRODO
La saldatura con elettrodo rivestito (MMA : Manual Metal Arc), anche identificata col termine SMAW (Shielded Metal Arc), è il procedimento più versatile e antico che consiste nel mantenere acceso un arco elettrico tra un "consumabile" ricoperto da un rivestimento e il pezzo da saldare.
Le gocce di metallo fuso che si staccano dall'elettrodo vengono trasferite attraverso l'arco nel bagno di fusione mentre contemporaneamente i gas prodotti dalle polveri del rivestimento le proteggono dall'atmosfera. La scoria fusa galleggia sopra il bagno di fusione e lo protegge dall'atmosfera durante la solidificazione. La scoria deve essere rimossa dopo ogni passata. Tra le centinaia di tipi di elettrodi esistenti, sono da segnalare quelli che apportano elementi di lega per migliorare le caratteristiche di durezza, resistenza meccanica e tenacità del giunto saldato. La saldatura manuale con elettrodo rivestito trova le sue maggiori applicazioni nelle strutture metalliche, costruzioni navali e carpenterie generiche. Nonostante sia un processo abbastanza lento a causa del continuo cambio di elettrodo e rimozione della scoria, rimane comunque il più flessibile e consente di saldare anche con spazi di accesso molto limitati.
2] FILO CONTINUO
Nella saldatura a filo continuo (GMAW :Gas Metal Arc Welding), anche conosciuta come MIG e MAG, si mantiene accesso un arco elettrico tra il filo pieno e il pezzo da saldare. L'arco e il bagno di fusione sono protetti da un flusso di gas attivo od inerte.
La saldatura MIG/MAG è decisamente più produttiva rispetto a quella con gli elettrodi dove occorre che il saldatore si fermi ogni volta per il cambio dell'elettrodo. Un altro vantaggio rispetto al procedimento SMAW è che non si hanno scarti di materiale in quanto non vi sono mozziconi di elettrodi da gettare via. Per ogni chilogrammo di elettrodi acquistato infatti , circa il 65 % del peso andrà a far parte del giunto saldato, mentre il resto è tutto scarto (scoria , mozziconi). L'impiego di fili continui sia pieni sia animati ha aumentato questa efficienza al 80-95 %. Questo procedimento viene largamente impiegato per strutture metalliche leggere o medio peso in acciaio al carbonio e per strutture in alluminio o leghe di alluminio.
3] FILO ANIMATO
Il procedimento con i fili animati (FCAW: Flux Cored Arc Welding) è molto simile a quello MIG/MAG per quello che riguarda il processo e gli impianti di saldatura utilizzati. L'unica differenza risiede nel fatto che il filo continuo non è pieno ma consiste di una piattina di metallo che avvolge un'anima di polveri (flusso). Prima di prendere la forma circolare definitiva, la piattina metallica assume una forma ad U. In questa fase si aggiungono le polveri e gli eventuali altri elementi di lega e si procede quindi alla successiva chiusura e "rullatura" del tubo fino ad ottenere la sezione circolare finale.
Come per il procedimento con filo pieno, anche con i fili animati un gas di protezione impedisce al bagno di fusione di venire a contatto con l'atmosfera. Il gas può essere fornito a parte, in aggiunta al filo animato, oppure può essere generato dalla decomposizione di alcune polveri contenute nel flusso (fili animati autoprotetti). Oltre al gas, i fili animati di tipo rutile e basici producono anche scoria che , come per gli elettrodi, deve essere rimossa tra una passate e l'altra.
4] TIG
Il procedimento TIG (Tungsten Arc Welding), noto anche come GTAW ( Gas Tungsten Arc Welding), è un procedimento di saldatura che usa un elettrodo non fusibile in tungsteno. L'elettrodo, l'arco e l'area circostante il bagno fuso sono protetti dall'atmosfera da un gas inerte. Se occorre aggiungere del materiale d'apporto, questo viene aggiunto in forma di bacchetta o filo continuo.
Il procedimento TIG consente di ottenere saldature di ottimo aspetto estetico e di qualità. Dato che non vi è scoria, il rischio di difetti quali inclusioni nel metallo d'apporto è assente e la superficie del cordone non richiede nessuna pulizia . Con il TIG si saldano praticamente tutti i metalli sia con procedimento manuale che automatico, sebbene il suo campo ottimale di applicazione sia quello dell'alluminio e degli acciai inossidabili. In particolare, è largamente impiegato nelle industria nucleare , chimica , aeronautica e alimentare.
5] SALDATURA AL PLASMA
La saldatura al plasma (PAW: Plasma Arc Welding) è un miglioramento del procedimento Tig che consente di ottenere maggiori benefici in termini di protuttività.
Diversamente dal tradizionale processo Tig, vi sono due afflussi indipendenti di gas. Uno dei due gas avvolge l'elettrodo di tungsteno formando successivamente il nucleo centrale dell'arco al plasma. Il secondo gas invece ha solo il compito di proteggere il bagno di saldatura.
La saldatura al plasma si impiega in tre modi: 1. Microplasma welding, con correnti da 0.1 a 20A. 2. Medium-plasma welding, con correnti di saldatura da 20 a 100A 3. Keyhole welding, oltre i 100 A, dove l'arco al plasma penetra tutto lo spessore del giunto. Viene largamente utilizzata per giunti di elevatissima qualità nell'industria aeronautica, spaziale e chimica.
6] SALDATURA A RESISTENZA
Nella metà degli anni sessanta, la Esab acquisì la società Asea-Svets , società che sin dagli anni trenta sviluppava e produceva saldatrici a resistenza.
La Esab dispone oggi di una gamma completa di saldatrici a resistenza, dalla più piccola controllata saltuariamente e manualmente dall'operatore, a quella molto più complessa che serve per saldare in automatico le catene delle ancore per le navi. Nella saldatura a resistenza i metalli vengono uniti senza l'ausilio di materiale d'apporto, applicando pressione e la giusta intensità di corrente alla zona che deve essere saldata. La quantità do calore dipende dalla resistenza elettrica dell'area interessata. Quest'ultima è un importante fattore per questo processo di saldatura e ci consente di individuare i sotto elencati sottogruppi.
Principali processi di saldatura a resistenza: · saldatura per punti (spot welding) · saldatura a rilievo · saldatura a rulli · testa-testa a resistenza · testa-testa a scintillio
7] ARCO SOMMERSO
Nella saldatura ad arco sommerso (SAW: Submerged Arc Welding) si ha sempre l'accensione di un arco elettrico tra il pezzo da saldare e il materiale d'apporto, ma in questo caso entrambi gli elementi sono ricoperti da una apposito flusso (da cui il termine submerged = sommerso), che ne impedisce la visione diretta. Parte del flusso fonde formando la scoria mentre la parte residua viene recuperata e riutilizzata.
Benché vi siano tuttora torce manuali per l'arco sommerso, il suo impiego quasi esclusivo è con impianti completamente automatici. Per ulteriormente aumentarne la produttività si possono impiegare più fili contemporaneamente (fino a cinque). I campi di applicazione ottimali per la saldatura in arco sommerso sono quelli inerenti a pezzi lunghi o circolari, di spessore elevato ( maggiore di 25 mm), quali caldareria, impianti chimici e grosse strutture metalliche.
8] ELETTROSCORIA
Il princìpio di base iniziale è sempre quello che prevede la formazione di un arco elettrico tra l'elettrodo e il pezzo da saldare. Quando il flusso di copertura all'interno del giunto fonde, si crea un bagno fuso di scoria che aumenta progressivamente la sua profondità. Quando la temperatura della scoria fusa e la sua capacità conduttiva aumentano, l'arco si spegne e la corrente di saldatura viene portata dalla scoria fusa dove l'energia necessaria è prodotta per resistenza.
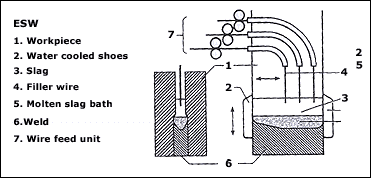
Il bagno di saldatura che si forma tra i lembi del giunto viene sostenuto da appositi supporti in rame raffreddati ad acqua che possono traslare o meno con la testa di saldatura. Uno o più elettrodi vengono utilizzati a seconda dello spessore che si deve saldare. E' prevista inoltre la possibilità di aggiungere anche una traslazione orizzontale dell'elettrodo stesso.
I vantaggi di questo procedimento sono:
· alta produttività · basso costo per la preparazione dei cianfrini · una sola passata, indipendentemente dallo spessore dei pezzi · assenza di distorsioni nelle giunzioni testa testa · minimo ritiro trasversale · basso rischio di cricche da idrogeno
Punti deboli di questo procedimento invece risiedono nel fatto che l'enorme energia utilizzata favorisce un lento raffreddamento che è la causa di un eccessivo ingrossamento dei grani nella zona termicamente alterata. Come conseguenza si ottengono bassi valori di resistenza agli urti alle basse temperature, aspetto questo non compatibile con i requisiti generali richiesti per manufatti saldati a garanzia del rischio di rotture fragili.
9] ELETTROGAS
La saldatura in elettrogas è una miglioria di quella in elettroscoria. Invece di utilizzare scoria fusa, come per i procedimenti Mig-Mag, il materiale d'apporto viene fuso da un arco che brucia in un gas di protezione. Questo procedimento è utilizzato per spessori di lamiera da 12 a 100 mm senza alcun movimento di oscillazione dell'elettrodo. La preparazione dei giunti può essere la semplice ed economica preparazione a lembi retti oppure la classica preparazione a V. Sono notevoli i benefici economici che si hanno rispetto alla tradizionale saldatura manuale in Mig-Mag impiegando questo procedimento per giunzioni verticali di notevole lunghezza ( serbatoi di stoccaggio, fasciami di navi).
Come per gli altri procedimenti con protezione gassosa, si impiegano sia fili animati che fili pieni, mentre i tipi di gas sono gli stessi di quelli utilizzati per il Mig-Mag. Paragonato al procedimento elettroscoria, il procedimento elettrogas causa una minore estensione della zona termicamente alterata (ZTA) e, come conseguenza, si ottegono migliori valori di resistenza agli urti alle basse temperature. Piccoli accorgimenti quali utilizzare lunghezze elevate di sporgenza libera di filo (stick out), consentono di aumentare la velocità di saldatura e ridurre la quantità di calore per cm2.
10] FRICTION STIR WELDING
Nuovo procedimento di saldatura che consente di penetrare completamente nella fase solida di un metallo (principalmente Alluminio), senza raggiungere il suo punto di fusione.
La Friction Stir Welding è stata inventata, brevettata e successivamente sviluppata per l'impiego nell'industria dal Welding Institute (TWI) di Cambridge (UK). Il processo utilizza un utensile cilindrico e un perno di sagoma opportuna che , ruotando a forte velocità, vengono spinti progressivamente sui due bordi dei pezzi da unire. Le due lamiere devono essere ancorate alla piastra di base per evitare che si possano spostare durante la lavorazione. Il calore che si sviluppa per attrito fra l'utensile e il materiale base rende quest'ultimo più duttile ma non è sufficiente a fargli raggiungere il punto di fusione. A raffreddamento avvenuto si nota la fase solida che unisce i due pezzi. L'impianto Friction Stir Welding è usato per unire fogli di alluminio senza alcun impiego di materiali d'apporto o gas di protezione. Spessori che variano da 1.6 a 30 mm possono essere saldati in unica passata senza avere difetti quali porosità o cavità interne. Sono state ottenute saldature di alta qualità con bassissime deformazioni anche con materiali considerati difficili da saldare con i tradizionali procedimenti per fusione quali alcune leghe di alluminio (2xxx,5xxx,6xxx,7xxx e 8xxx) e leghe Al-Li. Recentemente si è pure dimostrato che con l'impianto FSW è possibile unire altri metalli quali piombo, rame, magnesio e persino leghe in titanio.
Nota: Articolo di proprietà ESAB
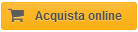