Applicazioni: modalità di posa e disegni applicativi
Il "tetto caldo" è una tipologia apllicativa ancora fra le più usate nelle coperture piane. In tale apllicazione la guaina è a diretto contatto sia con gli agenti atmosferici [vento, neve, pioggia] che con le eventuali sollecitazioni meccaniche che possono provocare danni rilevanti all'impermeabilizzazione, soprattutto se questa non è ben posata o non è idonea qualitativamente.
In estate una copertura assorbe in un giorno anche 5000 Kcal./mq. e la temperatura della struttura può raggiungere i +75°C, mentre in inverno l'assorbimento giornaliero è al massimo 1000 Kcal./mq. e la temperatura può scendere fino a -15°C.
Le radiazioni ultraviolette, che determinano l'innalzamento della temperatura, associate all'ossigeno favoriscono il processo di ossigenazione della membrana che perderà l'elasticità.
Ecco allora che è estremamente importante, oltre alla posa ed al colore dello strato finale della guaina [il nero assorbe e irraggia, il pietrisco dell'ardesia ha una bassa conducibilità e "rompe" l'angolazione dell'esposizione], l'armatura della membrana e la tipologia della mescola.
Ricordiamo inoltre che per poter essere utilizzato in strutture di questo tipo, l'isolante deve possedere oltre ad un notevole potere coibente, anche un'elevata resistenza meccanica, deve inoltre subire una modesta variazione dimensionale ed un limitato assorbimento d'acqua. Un utile riferimento nella scelta del materiale da impiegare per quanto riguarda le caratteristiche meccaniche e di stabilità richieste per queste applicazioni è dato dalla norma ISO DP 4898.4.
Essa distingue i materiali plastici cellulari per isolamento termico in tre categorie:
- 1a categoria: applicazioni non portanti, come isolamenti di intercapedini, coperture ventilate, soffitti, ecc.
Si richiede una resistenza minima alla compressione di 0,5 kg./cmq. al 10% di deformazione e una variazione dimensionale inferiore al 5% dopo 48 ore a 70°C.
- 2a categoria: applicazioni in cui l'isolante è soggetto a carichi limitati come nei pavimenti di edifici in cui si trova sottostante ad uno strato di ripartizione dei carichi o nelle coperture prefabbricate.
Resistenza alla compressione >= 1 kg./cmq. e resistenza alle deformazioni plastiche sotto un carico di 0,2 kg./cmq. per 48 ore a 80°C.
- 3a categoria: applicazioni tipiche come isolamento di terrazze parcheggio e fondazioni. Resistenza alla compressione >= 1,5 kg./cmq. e resistenza alle deformazioni plastiche sotto un carico di 0,4 kg./cmq. per 7 gg. a 70°C.
AVVERTENZE E MODALITÀ APPLICATIVE
PANNELLI dbx40® E/O dbx35®
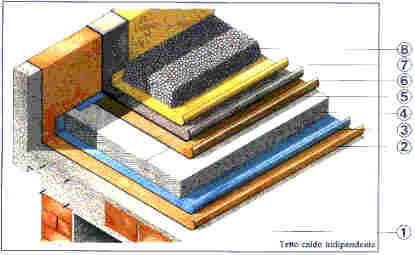 |
- Soletta portante
- Strato di compensazione in tessuto sintetico imputrescibile
- Barriera al vapore [film di polietilene]
- Pannelli isolanti dbx40® o dbx35® battentati, cm. 100x100 o cm. 100x50, spess. minimo consigliato cm. 4
- Eventuale strato separatore in carta lana o velo di vetro
- Strato impermeabilizzante [es. PVC flessibilizzato e stabilizzato ai raggi ultravioletti]
- Strato filtrante in feltro non tessuto in poliestere
- Strato di zavorramento in ghiaia di fiume o quadrotti prefabbricati
|
Applicando i pannelli dbx sotto la guaina si protegge la copertura dalle escursioni termiche e si rendono maggiormente confortevoli gli ambienti sottostanti.
Ogni elemento deve avere caratteristiche molto precise, interamente finalizzate alla diminuzione delle sollecitazioni degli strati sottostanti, che possono indurre nello strato esterno impermeabile.
A tal fine, ad esempio, la struttura portante non deve avere luci eccessive - secondo norma DIN 18550 - e lo strato isolante deve essere di ottima qualità, con minime variazioni dimensionali, essere resistenti alla compressione, con una durata pressoché illimitata nel tempo, come i pannelli dbx40® e dbx35®.
Omologati, a celle chiuse, non assorbono acqua per capillarità ed hanno un potere isolante che rimane inalterato nel tempo, anche nelle condizioni ambientali più sfavorevoli.
- Pulire l'estradosso del massetto, asportando eventuali grumi di cemento che alterano la planarità di posa.
- Appllicare un eventuale strato di compensazione in tessuto sintetico imputrescibile.
- Posare il film di polietilene.
- Adagiare i pannelli isolanti dbx40® o dbx35® misure cm. 100x100 o cm. 100x50 battentati, spessore appropriato.
- Eventuale strato separatore in carta lana o velo di vetro.
- Strato impermeabilizzante.
Se la guaina è saldata totalmente, durante le dilatazioni proprie della struttura e dell'isolante, si allunga [Fig. 1/A].
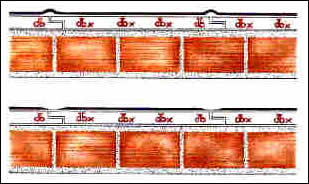 |
Fig. 1/A |
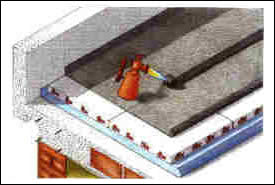 |
Fig. 1/B |
In seguito ad un calo di temperatura, si ritira assottigliandosi. Tali movimenti indeboliscono nel tempo lo strato impermeabilizzante fino a provocarne la rottura.
Per evitare ciò, occorre posare strisce tipo "tagliamuro" sui giunti, sfiammando i bordi [Fig. 1/B].
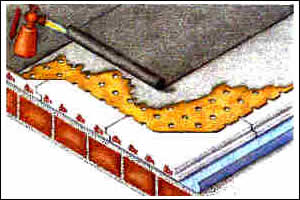 |
Se le condizioni atmosferiche lo permettono [poco vento], si consiglia di fissare semplicemente la guaina alla scossalina. È possibile sfiammare l'impermeabilizzazione direttamente sul dbx avendo cura che questi non venga a contatto immediato con la fiamma. Esiste un metodo un po' impegnativo che risponde a tale esigenza. Si prepara una mescola di catrame ossidato e si lascia un po' raffreddare oppure si utilizza catrame freddo [all'acqua] e la si stende con un spazzolone su un apposito cartone forato posato sul coibente [Fig. 1/C].
|
Fig. 1/C |
|
Si stende infine il rotolo impermeabilizzante sfiammandolo ove occorre.
Qualora si voglia stendere la guaina in due strati, occorre fare attenzione a posarli entrambi per lo stesso verso, infatti in caso contrario le dilatazioni "opposte" che si verificherebbero danneggerebbero irrimediabilmente l'impermeabilizzazione. Posare lo strato di zavorramento: ghiaia sfusa, [spessore minimo di 8-10 cm., diametro medio 1,5-3 cm.], quadrotti prefabbricati o realizzare una caldana qualora si voglia eseguire la pavimentazione.
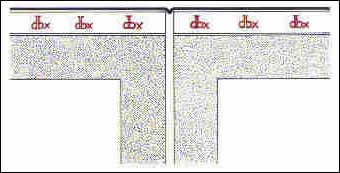 |
Particolare relativo alla posa della guaina sul coibente in prossimità del giunto di dilatazione.
|
Fig. 1/D |
|
PANNELLI AIPOR 30®, AIPOR 30RF®, POLIURETANO CON RIVESTIMENTO CON CARTA BITUMATA
A scelta si potrebbero usare anche tali isolanti. Naturalmente le caratteristiche tecniche sono differenti, come conseguentemente lo sarà il risultato finale.
Vi rimandiamo pertanto alle singole voci per una migliore verifica della tabella tecnica.
SISTEMA COVER FOAM®
L' evoluzione dell'edilizia moderna verso costanti innovazioni ha portato allo sviluppo di un'importante soluzione per tutte quelle problematiche legate alla posa del materiale coibente più lo strato impermeabilizzante.
Pertanto è stato studiato COVER FOAM®, una ricca gamma di accoppiati particolarmente raccomantata nelle costruzioni nuove o nei restauri di esistenti, civili o industriali.
La membrana bitume plastomero utilizzata per i pannelli o i rotoli COVER FOAM® e COVER FOAM/G® è particolarmente apprezzata per la notevole resistenza agli shock termici e all'invecchiamento; presenta inoltre un alto grado di allungabilità ed un'ottima capacità di conformazione alla struttura.
- Pulire l'estradosso del massetto, asportando eventuali grumi di cemento che alterano la planarità di posa.
- Applicare un eventuale strato di compensazione in tessuto sintetico imputrescibile o film di polietilene
Tipi di rotoli
Fig. 2
- Srotolare COVER FOAM 40® o COVER FOAM 35® o COVER FOAM 25®, con la membrana verso l'alto facendo attenzione ad installare ben accostati fra loro i successivi rotoli, onde evitare ponti termici.
- Incollarli con collanti o mastici a base di bitume a freddo oppure fisarli meccanicamente alla struttura portante mediante chiodi o tasselli in metallo o plastica.
La posa può essere anche a secco in totale indipendenza qualora sia previsto uno zavorramento nello strato di finitura.
- Per non incrociare i sormoti sfalsare la lunghezza dei rotoli.
- Posare un successivo strato impermeabilizzante in senso opposto [in direzione delle bocchette di scolo] sfiammando le giunzioni.
- Con una spatola arrotondata, opportunamente riscaldata, comprimere la zona sormontata lisciandone i bordi per eliminare eventuali capillarità e per una totale sigillatura.
- In presenza di parapetti, continuare verticalmente la posa onde evitare infiltrazioni.
- Il secondo ed ultimo strato di membrana, posato nello stesso senso del primo a giunti sfalsati, è bene sia di tipo granigliato, eventualmente chiaro, per una migliore temperatura d'esercizio [sfiammare le giunzioni].
- Qualora la rifinitura della copertura sia effettuata con ghiaia sfusa di zavorramento, quadrotti prefabbricati o una caldana per una successiva pavimentazione, l'ultimo strato impermeabilizzante può non essere ardesiato.
Fig. 3
- Srotolare COVER FOAM 40/3 mm.® CON CIMOSA O COVER FOAM 35/3mm.® CON CIMOSA O COVER FOAM 25/3 mm.® CON CIMOSA, con la membrana rivolta verso l'alto facendo attenzione di accostare bene fra loro i rotoli, sormontando la cimosa sul rotolo successivo.
- Incollarli con collanti o mastici a base di bitume a freddo oppure fissarli meccanicamente alla struttura portante mediante chiodi o tasselli in metallo o plastica. La posa può essere anche a secco in totale indipendenza qualora sia previsto uno zavorramento nello strato di finitura.
- Per non incrociare i sormonti sfalsare la lunghezza dei rotoli.
- Con una spatola arrotondata, opportunamente riscaldata, comprimere la zona sormontata lisciandone i bordi per eliminare eventuali capillarità e per una totale sigillatura.
Fig. 4
- Posare un successivo strato impermeabilizzante in senso opposto [in direzione delle bocchette di scolo], di tipo granigliato per una migliore temperatura d'esercizio, sfiammando i bordi. Se la copertura non presenta nessuna pendenza onde evitare il formarsi di "vaschette" posare il manto finale nello stesso senso del rotolo.
- Qualora la rifinitura della copertura sia effettuata con ghiaia sfusa di zavorramento, quadrotti prefabbricati o una caldana per una successiva pavimentazione, l'ultimo strato impermeabilizzante può essere ardesiano.
- In presenza di parapetti, continuare verticalmente la posa onde evitare infiltrazioni.
* Utilizzando i rotoli con cimosa con spessore di mm. 3 della membrana si ha il vantaggio di realizzare un primo manto impermeabilizzante completo e conseguentemente utilizzare un solo strato impermeabilizzante di finitura [vedere fig. 3 rispetto fig. 2].
- Qualora esista l'esigenza di pareti verticali esterne da coibentare oltre che impermeabilizzare a ridosso della copertura piana, si posa un pannello di COVER FOAM 40/3 mm.® o COVER FOAM 35/3 mm.® o COVER FOAM 25/3 mm.® con o senza battente, con o senza cimosa, lungo la parete fissandolo meccanicamente o con collanti.
- Si procede poi alla posa orizzontale comprimendo con una spatola arrotondata la linea di giunzione dei due manufatti [fig. 4].
- Per meglio fissare la giunzione ed in qualunque caso si vogliano evitare affaticamenti della membrana in prossimità di angoli a 90°, posare un "pezzo speciale" a triangolo [o altra forma necessaria] in lana di roccia FORTLAN® sopra COVER FOAM® coprendolo con una striscia di membrana a mo' di giunzione e/o procedere direttamente alla posa del successivo strato impermeabilizzante.
Tipi di pannelli
Fig. 5
- Posare COVER FOAM 40/3 mm.® IL BATTENTATO o COVER FOAM 35/3 mm.® IL BATTENTATO o COVER FOAM 25/3 mm.® IL BATTENTATO con la membrana rivolta verso l'alto accostando bene gli incastri fra loro.
- Fissarli meccanicamente con tasselli plastici alla struttura.
- Posare un successivo strato impermeabilizzante nel senso delle bocchette di scolo.
- Se la finitura è con pavimentazione, stendere una malta di allettamento di spessore circa una volta e mezzo quella del coibente, armata con rete elettrosaldata e procedere successivamente con la pavimentazione.
* Il pannello tipo battentato [brevettato] elimina i ponti termici ed è estremamente veloce nella posa
Fig. 6
- Posare i pannelli COVER FOAM 40/3 mm® CON CIMOSA o COVER FOAM 35/3 mm® CON CIMOSA o COVER FOAM 25/3 MM® CON CIMOSA, con la membrana rivolta verso l'alto accostando bene i giunti tra loro onde evitare ponti termici.
- Sormontare e comprimere bene la cimosa su ogni singolo pannello risvoltandola sul lato verticale in prossimità del parapetto.
- Fissare meccanicamente i pannelli con tasselli plastici alla struttura.
- Posare un successivo strato impermeabilizzante nel senso delle bocchette di scolo [non necessita il tipo ardesiato se la membrana è protetta da uno strato di finitura].
- Onde evitare infiltrazioni, proseguire la posa dello strato impermeabilizzante in presenza di parapetti.
Fig. 7
- Posare lo strato di ghiaia quale finitura [Fig. 6]. Questa può essere anche in quadrotti prefabbricati poggiati su supporti a base larga per non danneggiare lo strato impermeabilizzante [Fig. 7].
La posa dei pannelli è molto veloce e permette di adattare perfettamente il sistema in caso di perimetri anomali.
La cimosa e lo spessore mm. 3 della membrana accoppiata evitano la posa di uno strato successivo impermeabilizzante [uno anziché due] essendo così realizzato già un primo manto.
Fig. 8
- Posare COVER FOAM 40/3 mm.® CON CIMOSA BATTENTATO o COVER FOAM 35/3 mm.® CON CIMOSA BATTENTATO o COVER FOAM 25/3 mm.® CON CIMOSA BATTENTATO avendo cura che la membrana sia rivolta verso l'alto.
- Accostare bene gli incastri. Sormontare e ben comprimere la cimosa su ogni singolo pannello risvoltandola sul lato verticale in prossimità del parapetto.
- Fissare mecanicamente i pannelli con tasselli plastici alla struttura.
- Posare, sfiammandolo, un successivo strato impermeabilizzante nel senso delle bocchette di scolo, di tipo ardesiato chiaro per una migliore temperatura di utilizzo.
* Utilizzando i pannelli COVER FOAM® consigliati, si ottengono diversi vantaggi: adattabilità perfetta del sistema ad ogni perimetro anomalo, velocità di posa, eliminazione di uno strato di impermeabilizzazione di finitura, eliminazione di tutti i ponti termici.
Nota: By: di-bi S.p.A.